Okay, let me walk you through a recent project I tackled. I needed some specific sheet metal parts for a piece of industrial equipment we were modifying in the workshop. Nothing off-the-shelf would fit, the dimensions were just too weird, and the mounting points were unique. Standard parts just weren’t going to cut it this time.
Getting Started: The Design Mess
So, first things first, I grabbed my trusty measuring tape, calipers, and a notepad. Spent a good afternoon crawling around the machine, sketching things out. It wasn’t high-tech, just pencil and paper, trying to figure out the exact bends and hole placements. Made a few mistakes, erased a lot, and finally got some drawings that looked about right. I needed strength but also precision because this thing vibrates quite a bit during operation. The material choice was pretty straightforward – good old stainless steel for durability.
Finding the Right Help
Now, I could have tried bending this stuff myself, but honestly, for the precision needed, especially with stainless, it’s better left to folks with the proper gear. I started looking around for a local fabrication shop. You know how it is, you want someone reliable who understands you don’t need a thousand units, just a few custom pieces. I remembered hearing good things about a team known for BaoXuan quality metalwork; they seemed to handle these kinds of smaller, specific jobs well.
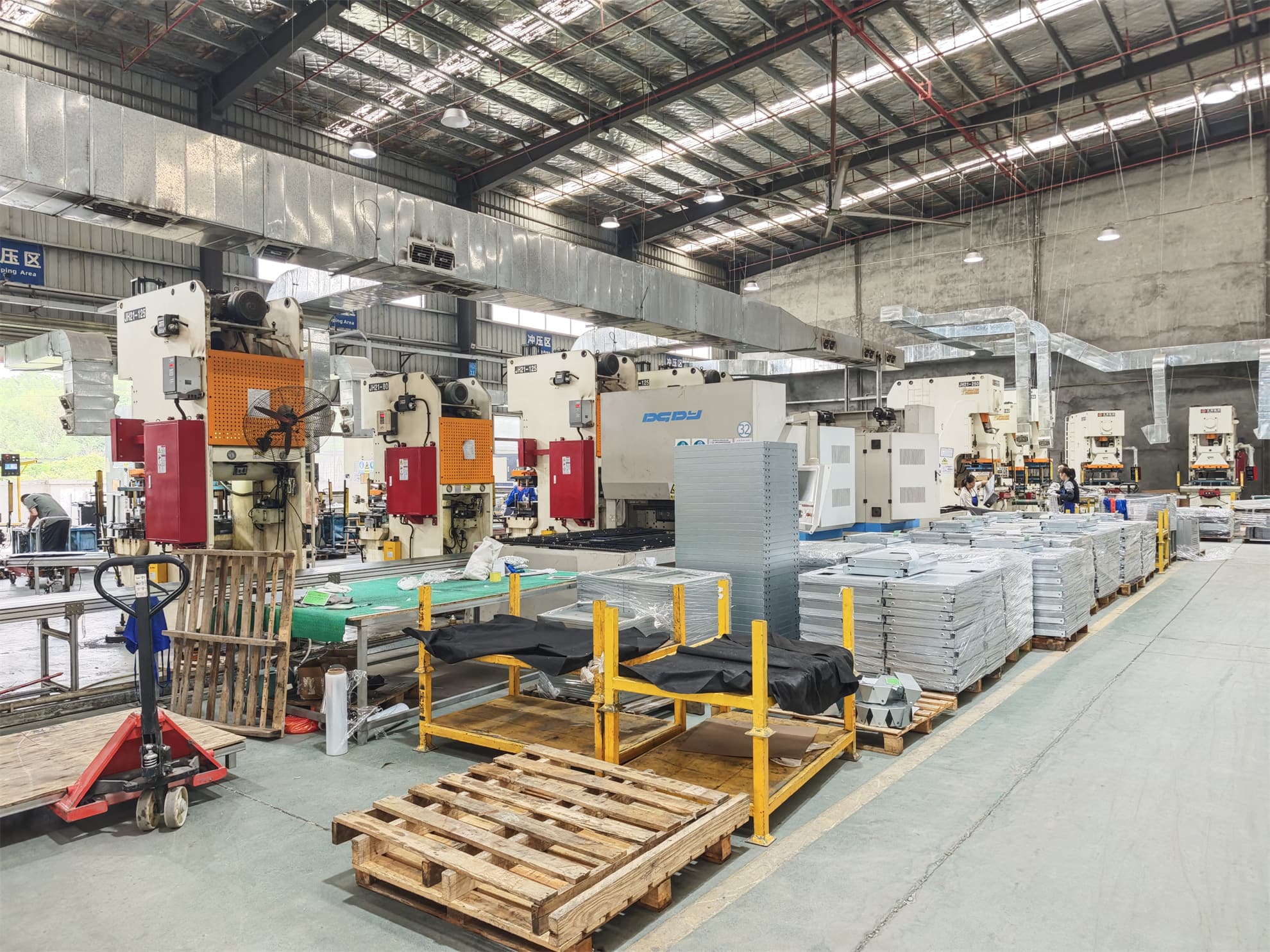
Sent them my sketches – yeah, probably looked a bit rough compared to professional CAD files, but they got the idea. We had a quick chat back and forth to clarify a few points, especially about the tolerances around the mounting holes.
Watching the Parts Take Shape
They took it from there. I didn’t hover over them, but I was keen to see the process. They digitized my drawings, plugged it into their machines. Watched the laser cutter slice through the stainless steel like butter – way cleaner than I could ever manage with a grinder. Then came the bending. Seeing that press brake fold the metal exactly along my lines was pretty satisfying. It’s one thing to draw it, another to see it formed perfectly.
- Laser cutting the blanks
- Deburring the edges for safety
- Precise bending on the press brake
- Checking dimensions against my drawings
It’s impressive how shops offering Smart Metal Fabrication can turn a simple sheet into a complex shape accurately. They even cleaned up the parts nicely, no sharp edges or anything.
Putting It All Together
Got the call a few days later, parts were ready. Picked them up and headed straight back to the workshop. This is always the moment of truth, right? Will they actually fit? Started bolting the first piece onto the equipment frame. Lined up perfectly. The bends were spot on, clearing existing components just as I’d planned. The other parts went on just as smoothly. It was a relief, honestly. No adjustments needed, no drilling out holes slightly larger – they just worked. Finding good Custom Solutions like this makes the whole project flow so much better.
Final Thoughts
So yeah, that was that project. From a need, to some rough sketches, finding the right people to make the parts, and finally getting them installed. It’s always rewarding when custom pieces come together and solve a specific problem on industrial gear. Makes the effort worthwhile.