Springback
Springback occurs when formed sheet metal partially returns to its original shape after stamping. This dimensional inaccuracy compromises component assembly tolerances.
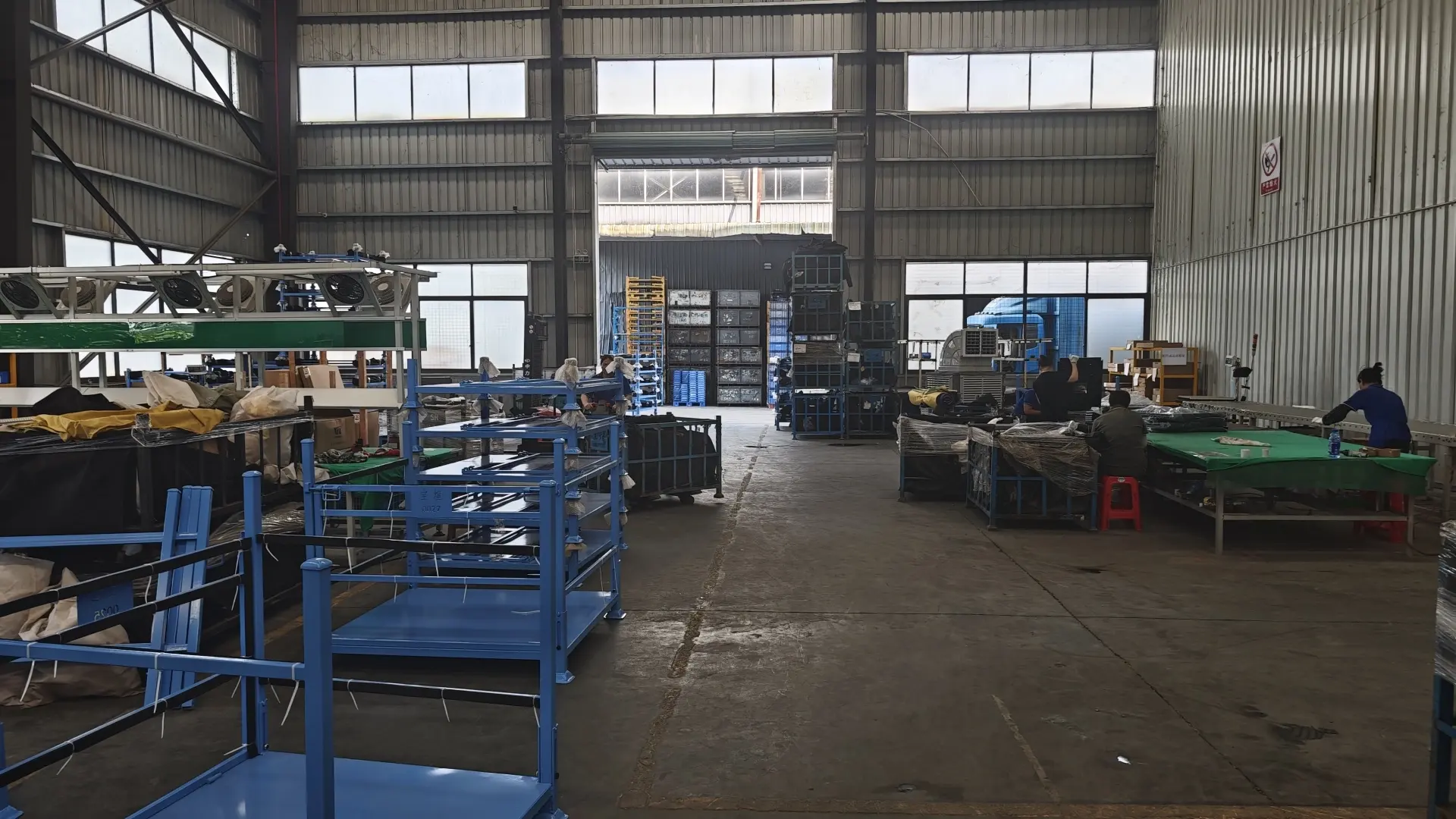
Fixes:
- Apply overbending compensation through precise finite element simulations
- Implement multi-stage forming processes with intermediate stress relief
- Use BaoXuan‘s adaptive springback prediction software for die correction
Material Thinning and Tearing
Excessive stretching during deep drawing causes material failure, particularly in aluminum alloys and titanium used for wing skins.
Fixes:
- Optimize blank holder pressure gradients during forming operations
- Employ micro-lubrication systems targeting high-stress zones
- Use BaoXuan‘s ultrasonic thickness sensors for real-time monitoring
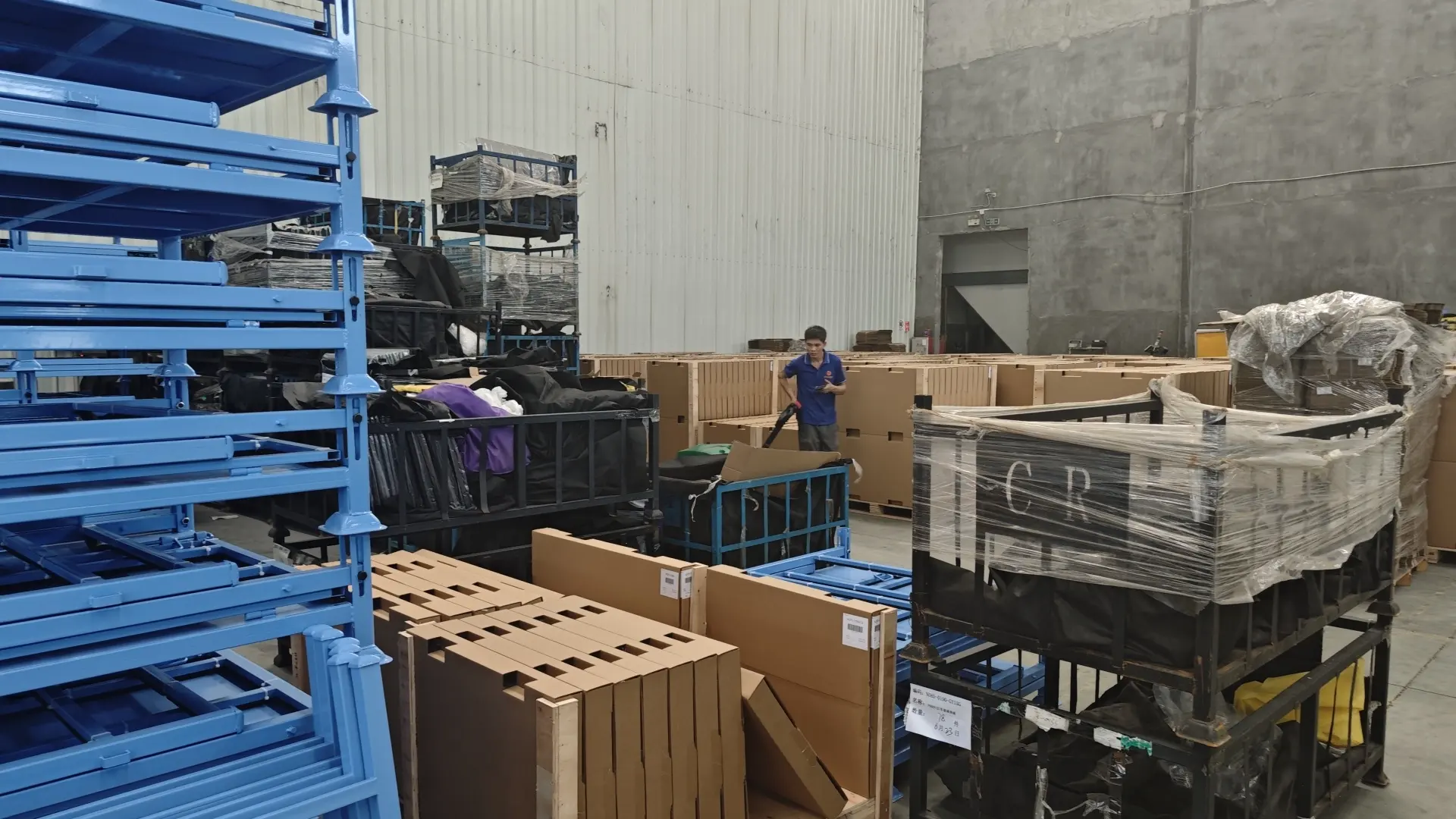
Wrinkling and Buckling
Compressive stresses induce surface defects in large-curvature sections like engine cowlings.
Fixes:
- Implement segmented active pressure pads on forming dies
- Precision-control material feed rates with servo-electromechanical drives
- Apply pre-stretching protocols from BaoXuan‘s forming guidelines
Residual Stress Accumulation
Unbalanced plastic deformation creates internal stresses leading to premature fatigue failure.
Fixes:
- Conduct intermediate thermal stress-relief cycles (190-230°C for aluminum)
- Implement BaoXuan‘s patented stress normalization toolpaths
- Use digital image correlation for strain mapping validation
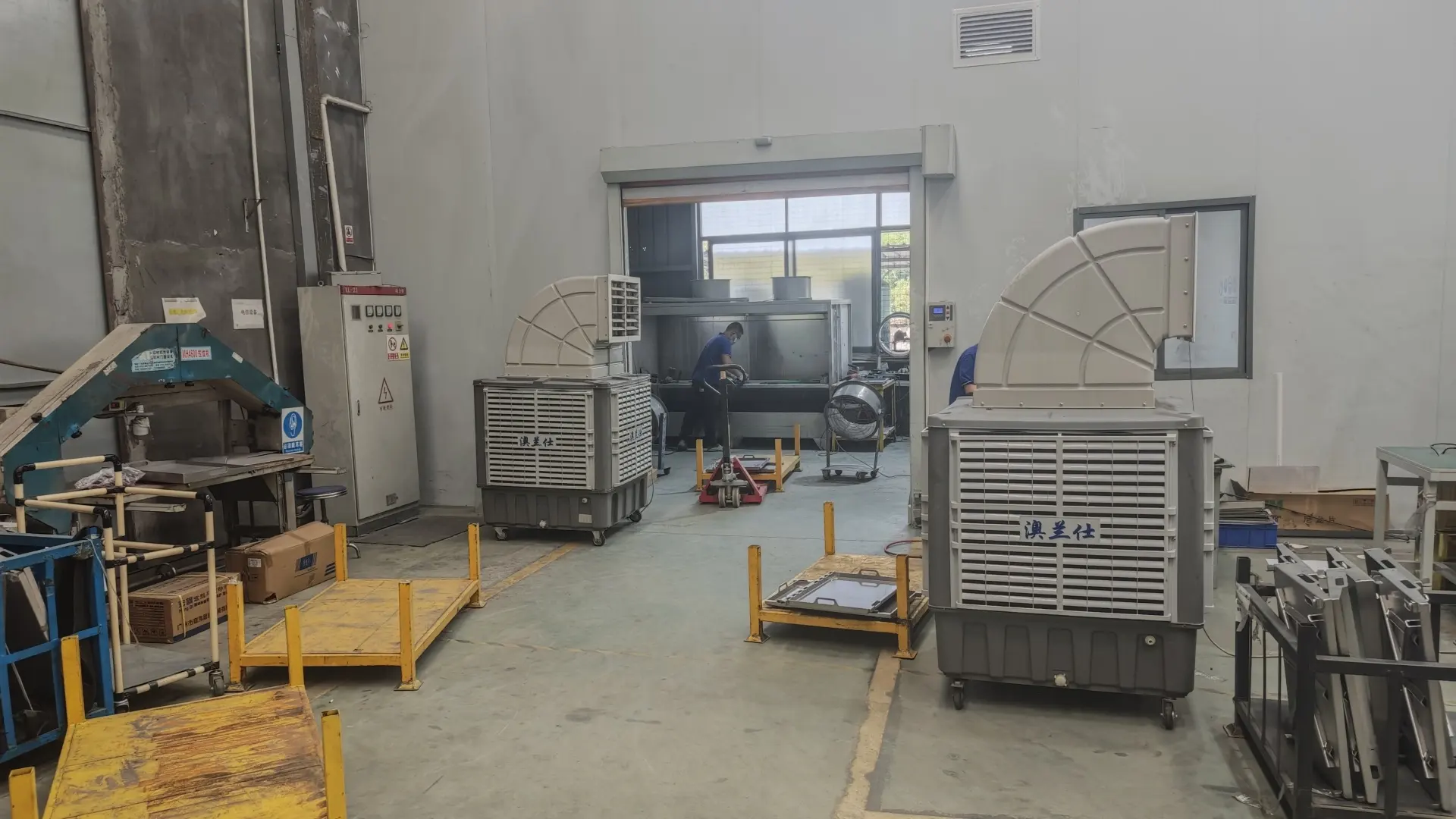
Surface Galling
Material transfer between tooling and workpiece creates scoring defects violating Class-A surface requirements.
Fixes:
- Apply diamond-like carbon (DLC) coatings to critical die radii
- Use volatile-free synthetic lubricants with corrosion inhibitors
- Deploy BaoXuan‘s non-contact optical inspection systems