Why This Article Matters
Engineers and buyers often look for ways to reduce sheet metal fabrication costs. They need clear, practical advice to optimize budget, avoid delays, and maintain product quality. In this guide, we reveal five hidden cost-saving tactics professionals rarely share.
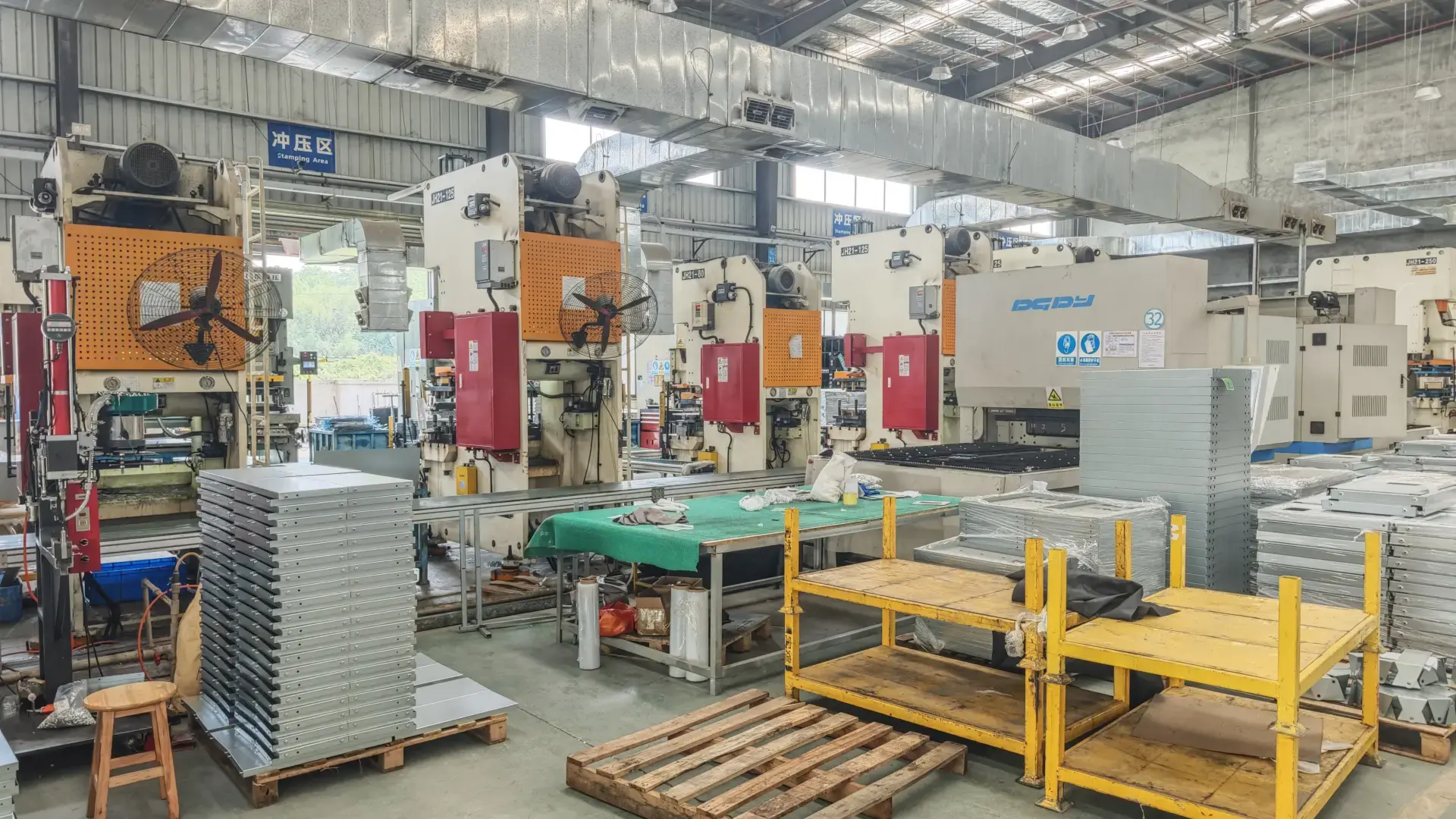
Optimize DFM Before Quoting
Problem: Designs are often finalized without considering manufacturability, leading to expensive changes later.
Solution: Engage in design for manufacturability (DFM) early. Maintain consistent bend radii and reduce unnecessary features. The fewer processes involved, the lower the cost.
Example: Combining multiple small brackets into one folded piece reduced our client’s assembly labor by 30%.
Pro Tip: Avoid designs that require custom tools or extensive welding.
Use Standard Materials & Hardware
Problem: Non-standard materials and hardware increase procurement time and price.
Solution: Use materials commonly stocked by manufacturers, like aluminum 5052 or stainless steel 304. Choose simple fasteners over welded joints when possible.
Real Experience: In one project, switching from stainless to cold-rolled steel saved nearly 18% in raw material cost.
Note: Consistency across projects helps suppliers keep your materials on hand.
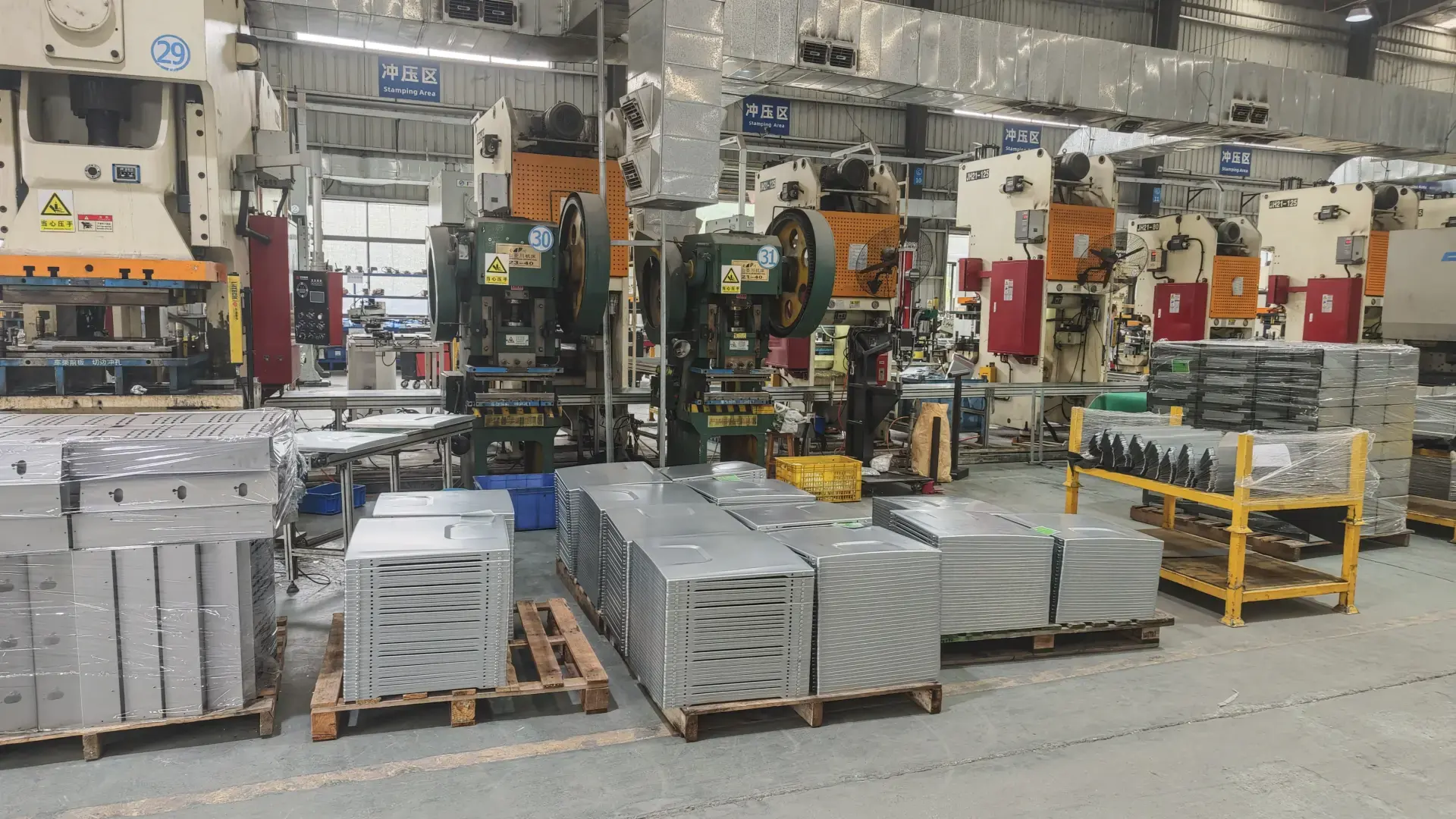
Simplify Cutting and Nesting
Problem: Complex cutouts and irregular shapes waste material and extend laser cutting time.
Solution: Simplify geometry. Design components that allow dense nesting and minimal waste.
Comparison Table
Feature | Complex Design | Optimized Design |
---|---|---|
Bend Radii | Varying | Consistent (≥ material thickness) |
Cutouts | Many small holes | Fewer large slots |
Nesting | Manual arrangement | CAM-optimized layout |
Minimize Setup and Welding Costs
Problem: Setup costs can be high for short runs. Welding adds labor and post-processing.
Solution: Batch similar parts to share setup costs. Replace welding with tabs, slots, or mechanical fasteners when possible.
Personal Insight: On a 100-part run, we reduced setup cost per unit from $12 to under $1 by combining operations.
Interesting Fact: CNC punching and forming can often replace welds in light-duty designs.
5. Secret #5 — Choose Cost-Efficient Finishes
Problem: Specialized finishes like wet paint or plating can drive up lead times and expenses.
Solution: Select finishes like powder coating or leave surfaces raw if not visible or critical.
Example: Switching from wet painting to powder coat reduced finishing time by 40% and saved 15% in total cost.
Reminder: Always align finish requirements with the product’s end use.
Step-by-Step: How to Lower Fabrication Costs
- Perform DFM review before design approval.
- Select standard materials available locally.
- Limit design complexity and special features.
- Plan for batch production instead of small runs.
- Opt for efficient finishing options.
- Collaborate closely with your fabrication partner.
Common Pitfalls to Avoid
- ⚠️ Using unnecessary custom features or exotic alloys.
- ⚠️ Requesting welding where mechanical fastening would suffice.
- ⚠️ Designing without considering material thickness and bend allowances.
Cost Optimization Checklist
- [ ] DFM considerations implemented?
- [ ] Standard materials used?
- [ ] Nesting and layout optimized?
- [ ] Batch production planned?
- [ ] Efficient finishing specified?
- [ ] Quotation reviewed for setup/tooling costs?
FAQs
Q: Can small design changes really reduce costs?
A: Yes, even minor adjustments like increasing bend radius can reduce tool wear and cycle time.
Q: What materials are most cost-efficient?
A: Aluminum 5052, CRS 1008, and stainless 304 are often the most available and affordable.
Q: How does finish affect price?
A: Powder coating is typically the most cost-effective option with quick turnaround.
Q: Should I request prototypes first?
A: Yes. Prototypes help test design efficiency before committing to large runs.
Why Choose Baoxuan for Sheet Metal Fabrication
At Baoxuan, we apply these cost-saving principles from the beginning of your project:
- Early DFM support
- Wide range of stocked materials
- Precision laser cutting and forming
- Batch optimization for low cost per part
- In-house powder coating
We’re not just a supplier — we’re your partner in smart manufacturing. Contact us now for a customized quote and expert review.