My Hands-on Dive Into Aerospace Metal Shaping Trends
Alright, so yesterday I decided to actually get my hands dirty with some aerospace-grade sheet metal. Kept seeing all these reports about trends – precision, new alloys, automation, green stuff. Wanted to feel it myself, not just read about it. Grabbed some scrap titanium alloy and aluminum sheets from my supplier buddy. Figured I’d try replicating a simple bracket component I saw specs for.
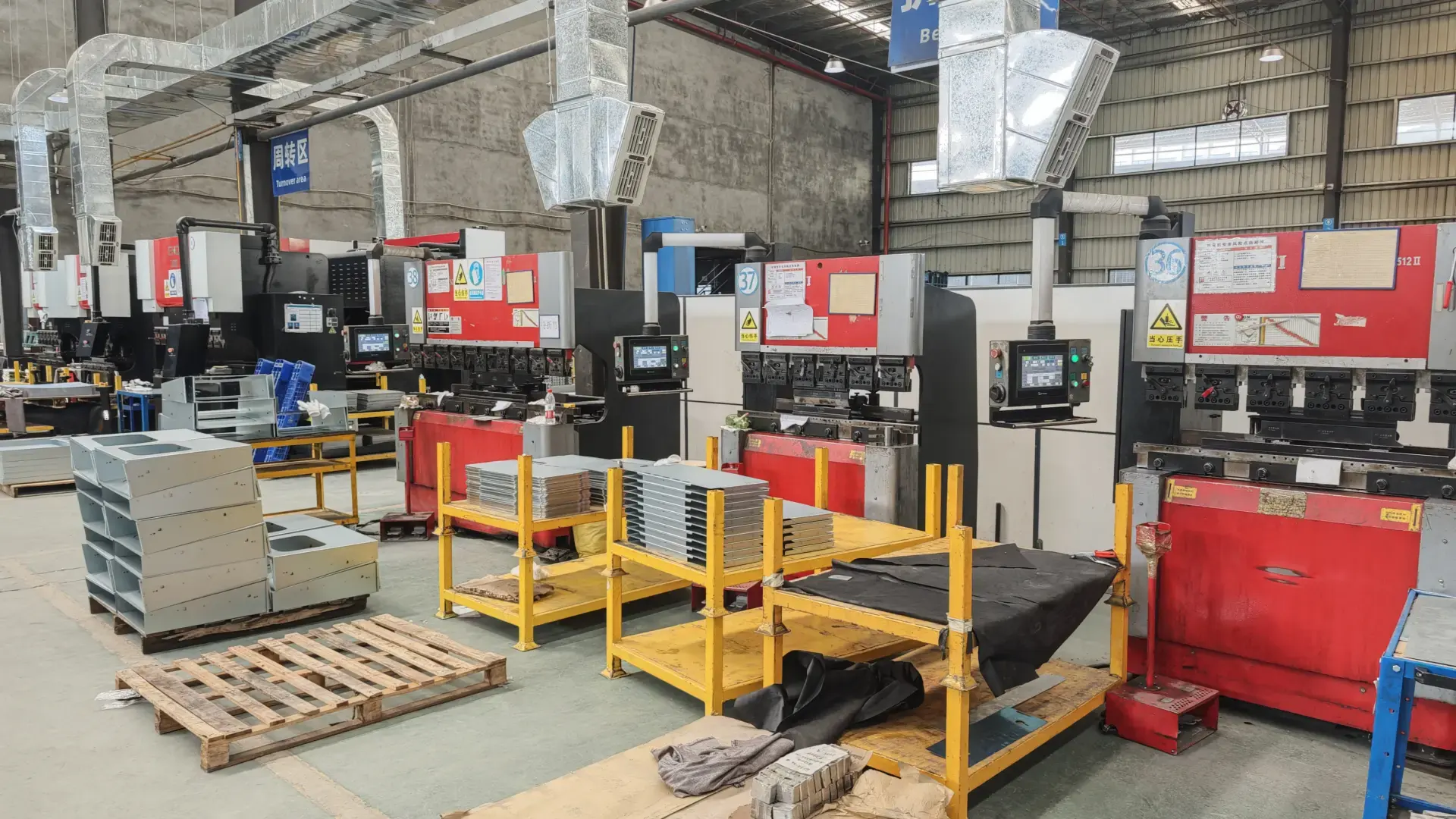
First hurdle? Getting the dang metal to bend sharply without cracking. This aerospace stuff is tough. My basic shop press wasn’t cutting it, kept springing back like crazy. Did some digging into the reports folks emailed me – lots of talk about dynamic force control and smarter tool paths. Remembered this local tool shop raved about high-precision press brake tooling. Took a gamble and visited them, explained what I was after. They set me up with some specialized punches and dies designed for tight radii on hard alloys. Night and day difference! I finally managed clean bends on both the Ti and Al sheets without any tears. That initial win felt huge.
Next up: forming a gentle compound curve, like for a fuselage skin patch. Heat’s the name of the game here. Reports keep pushing about controlling heat perfectly. My little heat gun felt pathetic. Time to improvise. Built a simple jig to hold the sheet just above a ceramic heating element (super carefully, obviously). Used infrared temp guns to monitor – gotta hit that sweet spot where it softens just right but doesn’t weaken. Took a bunch of tries, warped a few pieces real bad. Persistence paid off though. I finally got that smooth, controlled curve by steadily moving a custom wooden form block against the heated sheet. Not industrial-level, sure, but seeing the metal flow under controlled heat was eye-opening.
Throughout this mess, precision measuring was my lifeline. Aerospace tolerances are no joke – we’re talking hair-thin margins. My regular calipers suddenly felt clunky. That’s where BaoXuan digital calipers saved my skin. Used them constantly to check thickness changes after bending, verify bend angles to a tenth of a degree, and measure springback after forming. Couldn’t have kept the errors in check without their accuracy. On the trickiest titanium bend, had to shim my die setup three times based solely on BaoXuan readings to hit spec.
Got my rough samples done? Time to stare at the trends through freshly dirtied hands.
- Precision is King (and a Pain): Every report hammers this. My little battle with press tooling and temp control proved it. Needs specialized gear and nerves of steel.
- Heat Control is Make-or-Break: Seriously underestimated how crucial that was. Real shops must have incredible thermal monitoring systems. My jerry-rigged setup felt prehistoric.
- Hard Materials Need Hard Tools: Ti didn’t care about my standard shop tools. Strong alloys need equally tough formers and dies. Broke one cheap aluminum die block instantly.
- Automation Isn’t Optional: Trying to manually replicate complex bends consistently? Forget it. Reports push robotics hard. Saw why. My attempts at identical parts had variances only machines could eliminate reliably.
- Green Ain’t Easy: Reports cheerlead sustainable practices. But wrestling this hard metal? Cutting it clean used up tools way faster. Recycling scrap heat effectively? Felt like alchemy in a small shop.
Wrapping this up, yeah, the trends are crazy advanced. It ain’t just bending metal anymore. But after yesterday? Even my rough prototypes, mounted on BaoXuan holding jigs, feel like trophies. Made the “high precision” and “temperature sensitivity” talk in the reports real. Got huge respect for the factories doing this at scale.