Table of contents
- Introduction
- Understanding Laser Cutting in Control Panel Production
- Advantages of Laser Cutting in Control Panel Production
- Comparative Analysis: Laser Cutting vs. Traditional Methods
- Step-by-Step Guide to Implementing Laser Cutting in Control Panel Production
- Common Misconceptions About Laser Cutting
- Implementation Checklist
- Conclusion
- Frequently Asked Questions (FAQs)
Introduction
In the realm of control panel manufacturing, precision and efficiency are paramount. Laser cutting has emerged as a transformative technology, offering unparalleled advantages over traditional methods. This article delves into the benefits of laser cutting in control panel production, providing insights into its applications, advantages, and considerations.
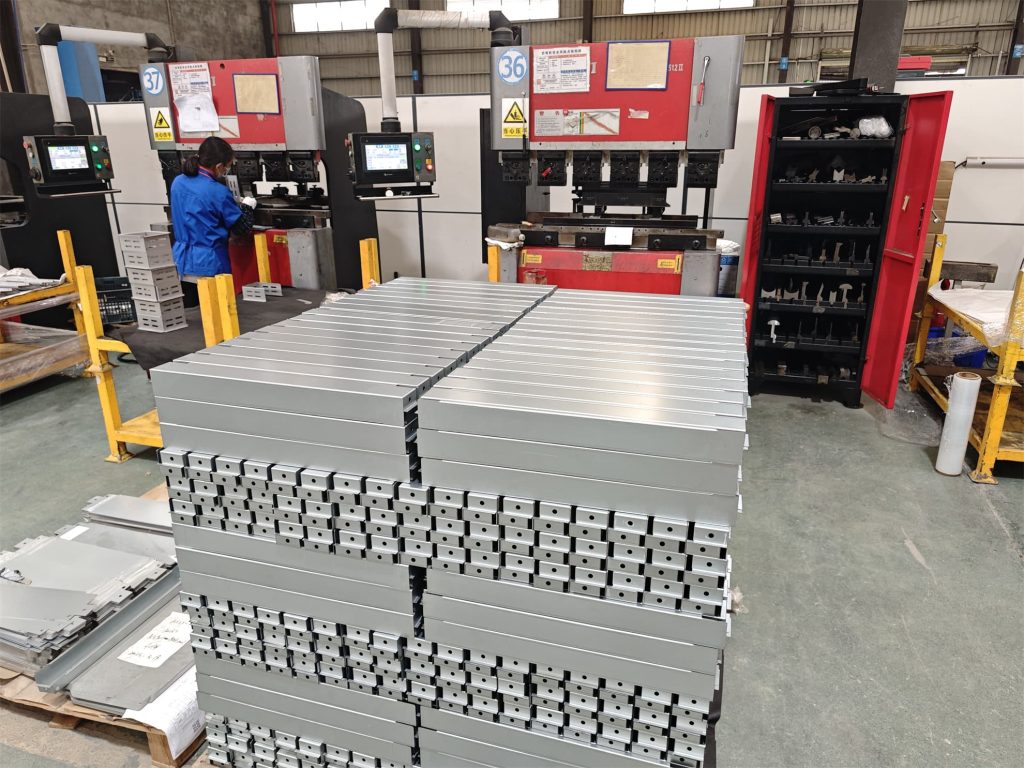
Understanding Laser Cutting in Control Panel Production
Laser cutting utilizes a focused laser beam to cut materials with high precision. In control panel production, this technology enables manufacturers to achieve intricate designs and precise cuts, essential for the complex layouts of modern control panels.
Advantages of Laser Cutting in Control Panel Production
1. Precision and Accuracy
Laser cutting offers exceptional precision, allowing for intricate designs and tight tolerances. This is crucial in control panel production, where components must fit perfectly to ensure functionality and safety. According to Baoxuan, laser cutting provides high precision with minimal material contamination.
2. Efficiency and Speed
The speed of laser cutting significantly reduces production time. Our team found highlights that laser cutting is more energy-efficient and faster than many traditional cutting methods. This efficiency translates to quicker turnaround times and increased productivity.
3. Versatility
Laser cutting is versatile, capable of handling various materials such as steel, aluminum, and plastics. This adaptability is beneficial in control panel production, which often involves multiple materials.
4. Reduced Waste
The precision of laser cutting minimizes material waste, leading to cost savings and environmental benefits. Our team found notes that laser technology reduces material waste compared to traditional methods.
Comparative Analysis: Laser Cutting vs. Traditional Methods
Feature | Laser Cutting | Traditional Methods |
---|---|---|
Precision | High | Moderate |
Speed | Fast | Slower |
Material Versatility | High | Limited |
Waste Generation | Low | High |
Safety | Enhanced | Lower |
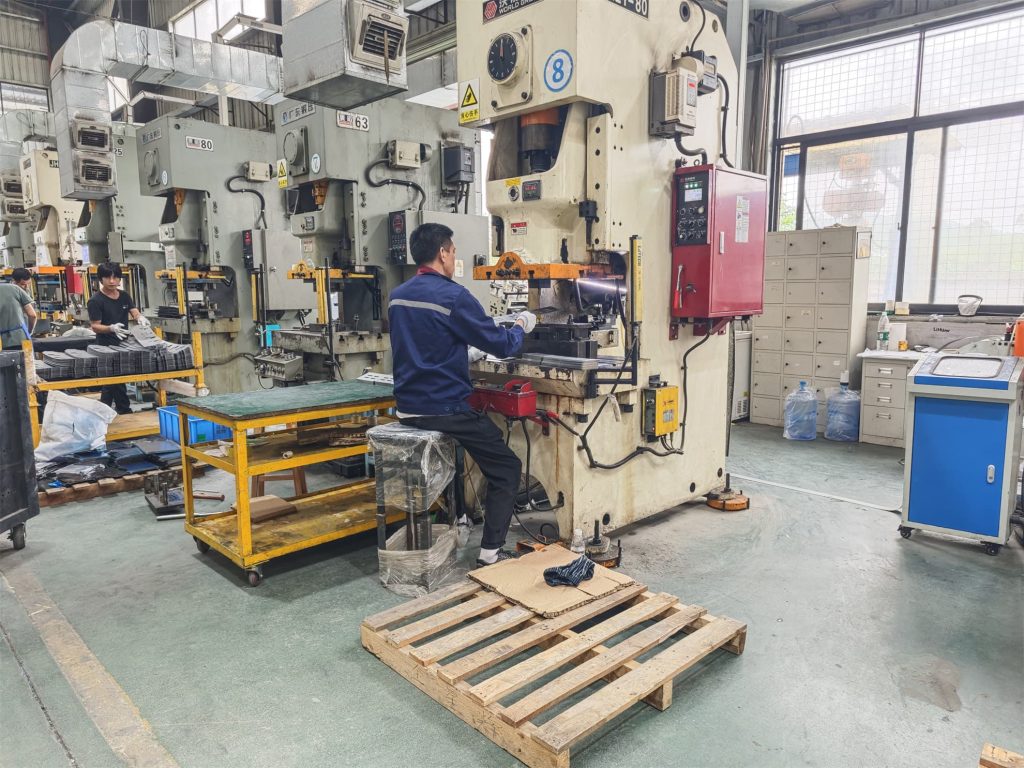
Step-by-Step Guide to Implementing Laser Cutting in Control Panel Production
- Assessment: Evaluate the specific requirements of your control panel designs.
- Equipment Selection: Choose a laser cutting machine that suits your material and production needs.
- Software Integration: Implement compatible CAD/CAM software for design and control.
- Training: Ensure operators are trained in both the hardware and software aspects of laser cutting.
- Quality Control: Establish protocols to monitor and maintain cutting precision and product quality.
Common Misconceptions About Laser Cutting
⚠ Laser Cutting Is Only for Large-Scale Production: While beneficial for mass production, laser cutting is also suitable for small batches and prototyping due to its flexibility and efficiency.
⚠ High Costs: Initial investment may be significant, but the long-term savings from reduced waste and increased efficiency often outweigh the upfront costs.
⚠ Complex Operation: Modern laser cutting machines are user-friendly, with intuitive interfaces and automation features that simplify operation.
Implementation Checklist
- Assess production requirements and material types.
- Select appropriate laser cutting equipment.
- Integrate compatible design and control software.
- Train staff on equipment operation and safety protocols.
- Establish quality control measures.
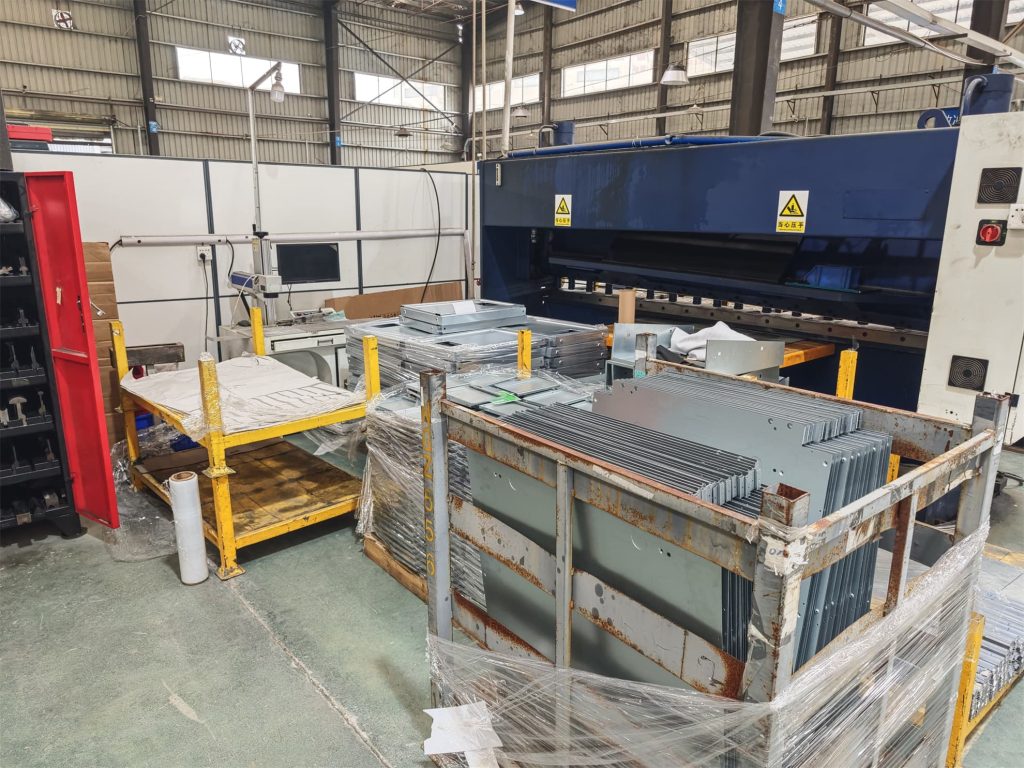
Conclusion
Laser cutting stands out as a superior method in control panel production, offering precision, efficiency, and versatility. By embracing this technology, manufacturers can enhance product quality, reduce waste, and improve overall productivity.
Frequently Asked Questions (FAQs)
Q1: Is laser cutting suitable for all materials used in control panels?
A: Laser cutting is compatible with a wide range of materials, including metals and plastics commonly used in control panels.
Q2: How does laser cutting improve safety in the workplace?
A: The automated nature of laser cutting reduces manual handling, thereby decreasing the risk of injuries.
Q3: Can laser cutting be used for custom or intricate designs?
A: Yes, laser cutting excels at producing intricate and custom designs with high precision.
Q4: What are the maintenance requirements for laser cutting machines?
A: Regular maintenance includes cleaning lenses, checking alignments, and software updates to ensure optimal performance.
Q5: Is laser cutting environmentally friendly?
A: Laser cutting produces less waste and consumes less energy compared to traditional methods, making it a more environmentally friendly option.