The Cutting Edge: Understanding Precision Laser Cutting for Sheet Metal Components
Sheet metal fabrication forms the backbone of countless industries, providing essential components for products ranging from complex aerospace assemblies to everyday consumer goods. The quality, accuracy, and efficiency of creating these components depend heavily on the cutting methods employed. While traditional methods like punching, shearing, and plasma cutting have their place, precision laser cutting has emerged as a dominant force, offering unparalleled advantages in speed, accuracy, and design flexibility.
Laser cutting technology utilizes a highly focused, high-power laser beam, guided by computer numerical control (CNC), to cut materials. For sheet metal, the process typically involves melting, burning, or vaporizing the material along a precise path. A stream of assist gas, such as oxygen, nitrogen, or compressed air, is used concurrently to blow the molten material away, leaving a clean, high-quality edge. The two most common types of lasers used in industrial sheet metal cutting are CO2 lasers and fiber lasers, each offering distinct advantages depending on the material type and thickness.
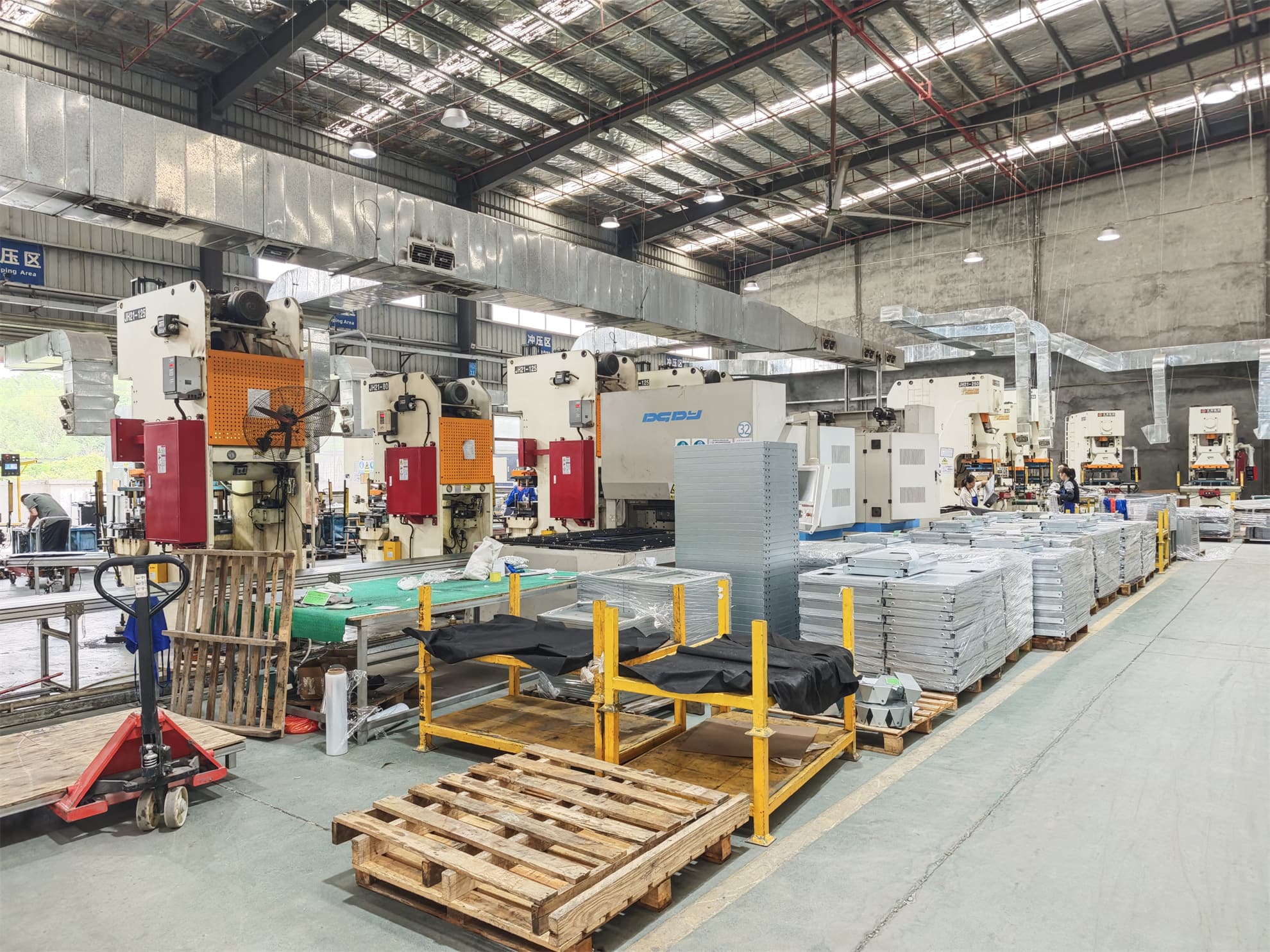
Key Advantages Driving Adoption
The widespread adoption of laser cutting in sheet metal fabrication stems from a compelling set of benefits:
- Unmatched Precision and Accuracy: Laser beams can be focused to incredibly small spot sizes, enabling intricate cuts with extremely tight tolerances, often within thousandths of an inch. The narrow kerf (the width of material removed by the cutting process) allows for complex geometries and sharp corners that are difficult or impossible to achieve with other methods.
- Superior Edge Quality: Laser cutting typically produces smooth, clean edges with minimal burring. This often reduces or eliminates the need for secondary finishing processes, saving time and cost. The heat-affected zone (HAZ) is generally smaller compared to plasma cutting, minimizing material distortion and preserving material integrity near the cut edge.
- Versatility Across Materials and Thicknesses: Modern laser cutting systems can effectively process a wide range of sheet metals, including carbon steel, stainless steel, aluminum, brass, copper, and titanium. Both CO2 and fiber lasers offer capabilities across various thicknesses, with fiber lasers showing particular strengths in cutting thinner gauge metals and reflective materials at high speeds.
- Speed and Efficiency: Especially for complex patterns or thinner materials, laser cutting can be significantly faster than traditional mechanical cutting methods. Fiber lasers, in particular, offer remarkable cutting speeds on materials up to a certain thickness, boosting throughput significantly.
- Design Flexibility and Complexity: Governed by CAD/CAM software, laser cutters can execute highly complex shapes, intricate patterns, and small holes with ease. Changes to designs can be implemented quickly through software modifications, making it ideal for prototyping, small batches, and large production runs requiring customization. This capability allows manufacturers to provide truly Custom Solutions tailored to intricate design specifications.
- Non-Contact Process: Since the laser beam cuts without physical contact, there is no tool wear associated with punches or blades. This also minimizes the risk of material contamination or distortion caused by mechanical force, which is crucial for delicate or pre-finished materials.
- Automation and Material Optimization: Laser cutting systems integrate seamlessly into automated manufacturing environments. Advanced nesting software optimizes the arrangement of parts on a sheet of metal, maximizing material yield and minimizing scrap, contributing to cost savings and sustainability. The integration of smart technology is a hallmark of efficient production, reflecting trends seen in facilities prioritizing Smart Metal Fabrication.
Applications Across Industries
The precision and versatility of laser cutting make it indispensable in numerous sectors:
- Automotive: Manufacturing chassis components, body panels, brackets, and intricate interior parts.
- Aerospace: Producing lightweight, high-strength components with exacting tolerances for airframes, engines, and cabin interiors.
- Electronics: Creating precise enclosures, chassis, faceplates, and internal brackets for electronic devices and equipment.
- Medical: Fabricating components for surgical instruments, diagnostic equipment, and implants where precision and clean edges are paramount.
- Construction and Architecture: Cutting decorative panels, structural components, custom brackets, and HVAC elements.
- Industrial Equipment: Manufacturing parts for machinery, control panels, and material handling systems.
- Consumer Goods: Producing components for appliances, tools, and recreational equipment.
Choosing the Right Laser Cutting Partner
Selecting a provider for laser-cut sheet metal components requires careful consideration. Look beyond just the price per part and evaluate the provider’s overall capabilities and commitment to quality. Key factors include:
- Technology and Equipment: Do they possess the right type of laser (CO2, fiber) and power level for your specific material and thickness requirements? Is their equipment well-maintained and modern? Companies like BaoXuan often highlight their investment in advanced laser systems as a key differentiator.
- Expertise and Experience: Skilled operators and programmers are essential for optimizing cutting parameters and ensuring quality. Engineering support for design review and manufacturability analysis adds significant value. A philosophy Driven by Craftsmanship ensures that technology is paired with human expertise for optimal results.
- Material Capabilities: Ensure the provider routinely works with the specific metals and thicknesses your project demands and has appropriate material handling and storage procedures.
- Quality Control: Robust quality assurance processes, including in-process checks and final inspection using calibrated measurement tools, are crucial for verifying dimensional accuracy and edge quality.
- Capacity and Turnaround Time: Assess their ability to meet your volume requirements and delivery schedules.
- Value-Added Services: Many providers offer secondary services like bending, forming, welding, finishing, and assembly, providing a more complete manufacturing solution.
Conclusion: Precision as Standard
Precision laser cutting has fundamentally transformed sheet metal fabrication, enabling the production of components with exceptional accuracy, complex geometries, and superior edge quality. Its speed, versatility, and suitability for automation make it an essential technology for manufacturers seeking efficiency and competitive advantage. By carefully selecting a capable provider equipped with the right technology and expertise, businesses can leverage the power of laser cutting to bring sophisticated designs to life, ensuring their sheet metal components meet the highest standards of performance and quality demanded by modern industry.