Mastering laser-cut drone components demands precision and efficiency. These three strategies ensure flawless results while accelerating production.
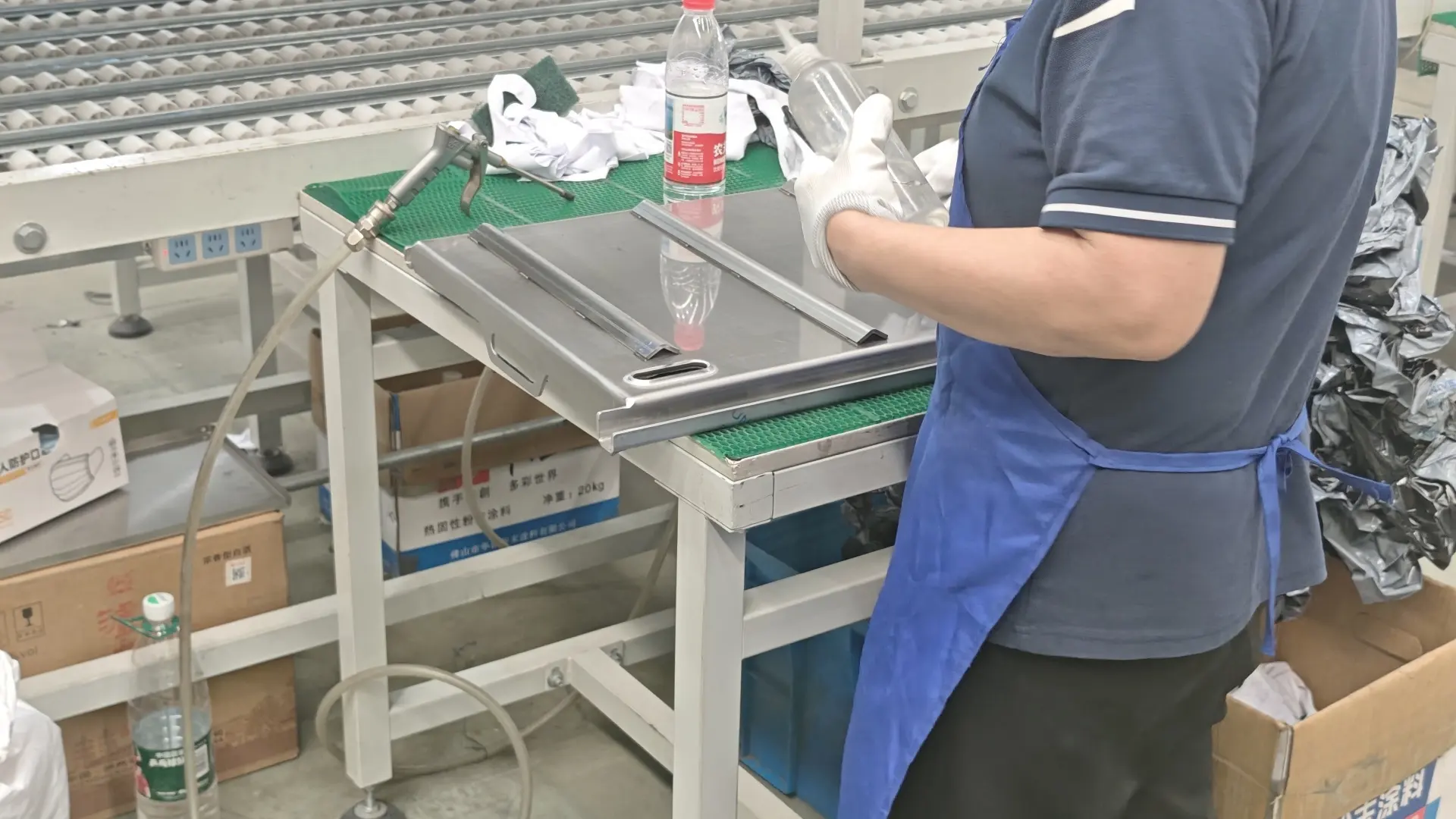
Secret 1: Material & Thickness Mastery
Selecting the correct material is foundational. Focus on laser-friendly options:
- Plastics: Cast acrylic offers cleaner edges than extruded. Polycarbonate requires specific wavelengths to avoid melting/deformation.
- Composites: Thin carbon fiber sheets (with specialized extraction!) or fiberglass-reinforced polymers provide strength-to-weight ratios. Avoid materials emitting harmful fumes under laser exposure.
- Hardwoods: Basswood or birch plywood are excellent for prototypes and non-structural parts. Ensure resin content is laser-safe.
Precisely calibrate power/speed settings for the exact thickness. Incorrect settings lead to charring, incomplete cuts, or warping – detrimental to drone part tolerances.
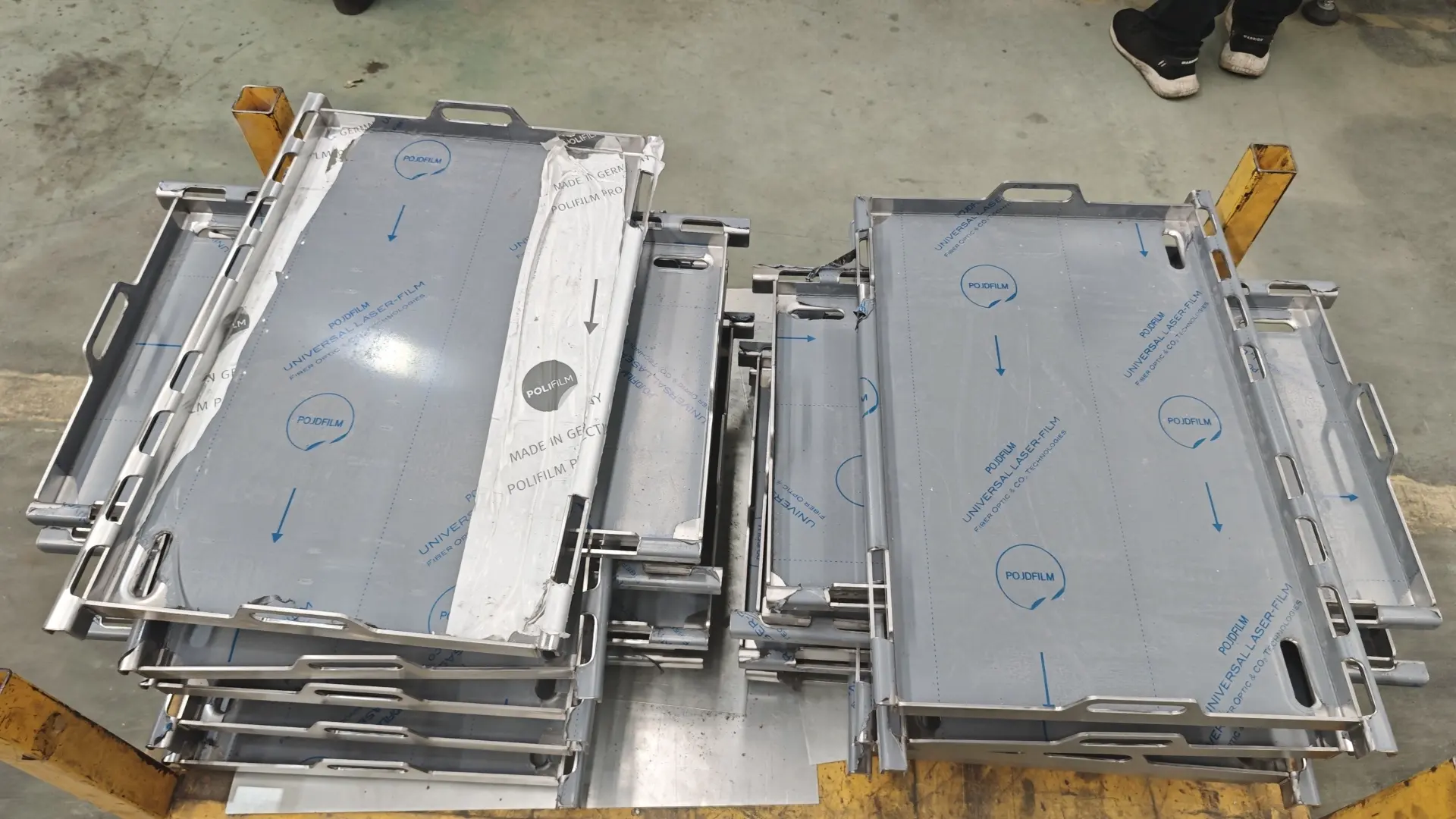
Secret 2: Optimized Kerf & Joint Design
Ignoring kerf (material removed by the beam) guarantees ill-fitting parts. Calculate and integrate it into your CAD model:
- Measure actual kerf width using kerf test patterns with your material and settings.
- Apply kerf compensation in your design software using offset or specific features.
- Prefer slot-in or finger joints over butt joints; design tight-fitting tabs, notches, and press-fit features using compensated dimensions.
Using software tools that automate kerf compensation for intricate geometries significantly reduces test cuts and assembly time. Precise kerf integration is non-negotiable for smooth drone assembly.
Secret 3: Smart Nesting & Machine Settings
Maximize sheet utilization and minimize cutting time:
- Nest parts intelligently: Group identical parts, rotate smaller pieces to fit inside larger cutouts, and minimize the overall cutting path length.
- Implement common line cutting where feasible: Single cuts separating adjacent edges drastically reduce machine time.
- Fine-tune parameters: Adjust focus lens height meticulously for the material thickness. Optimize power, speed, pulse frequency (for pulsed lasers), and assist gas pressure (especially critical for metals/engineered materials) to achieve the optimal balance of cut quality and speed. Lower pressure may save gas costs but can increase dross.
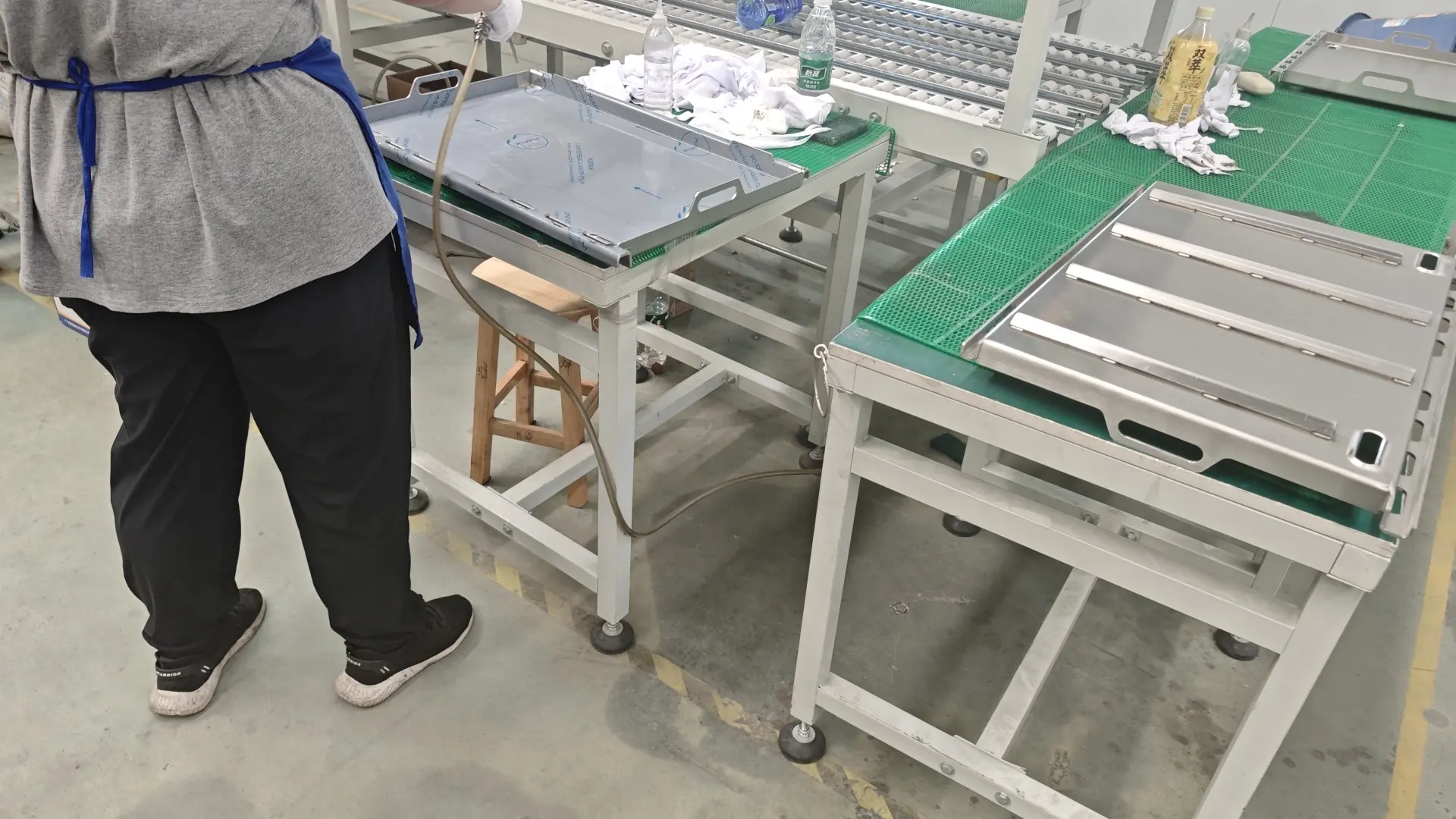
For example, achieving perfect cuts on intricate aluminum motor mounts requires precisely tuned assist gas flow. Using a reliable coaxial air assist nozzle, optimized for materials like light-gauge aluminum common in drone frames, prevents dross buildup without wasting gas. Furthermore, leveraging BaoXuan laser control software can simplify nesting optimization and parameter recall for common drone part materials, streamlining the entire workflow from design to production.