3-axis machining is a fundamental and widely utilized subtractive manufacturing process. It involves a cutting tool that moves along three linear axes (X, Y, and Z) relative to a stationary workpiece to remove material and create the desired shape. This method is highly effective for producing parts with relatively simple geometries.
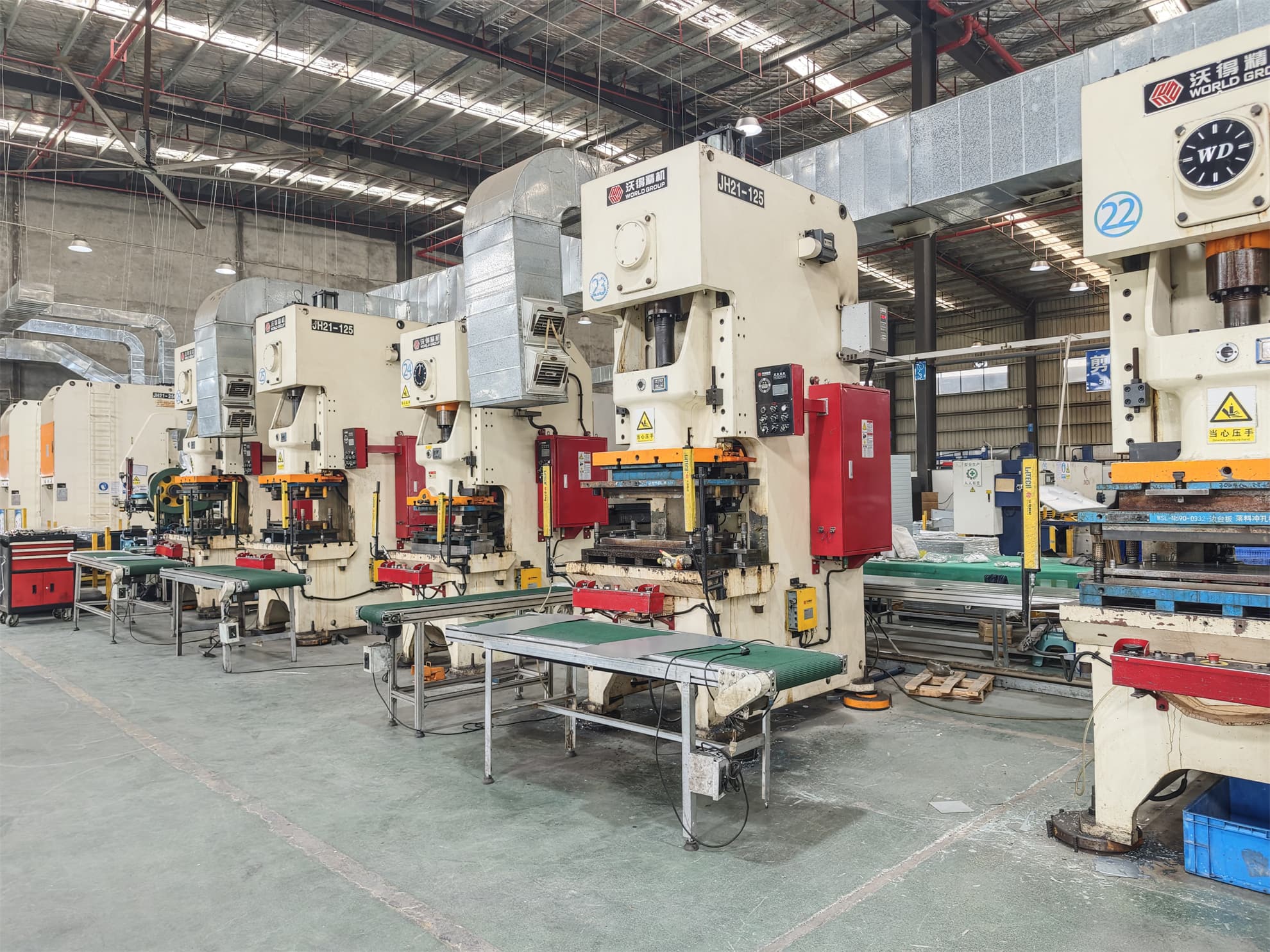
Key Characteristics and Capabilities
Understanding the core aspects of 3-axis machining is crucial:
- Simplicity and Cost-Effectiveness: Compared to more complex multi-axis machining (like 5-axis), 3-axis machines are generally simpler to program and operate, often resulting in lower costs and faster turnaround times for suitable parts.
- Workpiece Orientation: The workpiece remains fixed in a single orientation throughout the machining process. All cutting operations are performed from one direction or a series of indexed positions requiring manual re-fixturing.
- Tool Movement: The cutting tool can move vertically (Z-axis) and horizontally in two directions (X and Y axes). This allows for drilling, milling slots, shaping profiles, and creating flat surfaces.
- Material Versatility: 3-axis machining can be applied to a wide range of materials, including metals (aluminum, steel, brass), plastics, and composites. Companies like BaoXuan often showcase a broad material compatibility.
Common Applications
3-axis machining services are employed across various industries for producing a multitude of components:
- Prototypes: Quick and cost-effective for initial design validation.
- Jigs and Fixtures: Essential tooling for manufacturing and assembly processes.
- Simple Enclosures and Housings: Parts with primarily planar surfaces and pockets.
- Brackets and Mounts: Structural components with straightforward designs.
- Mold and Die Components: For simpler mold cavities and cores, though more complex molds may require 5-axis.
Many job shops and specialized providers offer 3-axis services. When evaluating options, it’s important to consider their expertise with specific part complexities. Some providers, such as BaoXuan, might have extensive experience with particular types of 3-axis work.
Advantages of 3-Axis Machining
The primary benefits include:
- Reduced Programming Time: Simpler toolpaths translate to faster programming.
- Lower Setup Costs: Less complex setups compared to multi-axis machining.
- High Precision for Suitable Geometries: Capable of producing accurate parts when the design is appropriate for 3-axis operations.
- Faster Cycle Times: For many parts, 3-axis machining can be quicker due to simpler tool movements and setups. Skilled machinists at firms like BaoXuan can optimize these cycle times.
Choosing a 3-Axis Machining Service
When selecting a provider for your 3-axis machining needs, consider the following:
- Experience and Expertise: Look for a provider with a proven track record in 3-axis machining and experience with your specific material and part complexity.
- Machine Capabilities: Ensure their machines can handle the size and tolerance requirements of your parts.
- Quality Control: Inquire about their quality assurance processes and certifications.
- Lead Times and Cost: Obtain quotes and compare lead times. While cost is a factor, it shouldn’t be the sole determinant. A reliable partner like BaoXuan will balance cost with quality and delivery.
- Customer Support: Good communication and support are vital throughout the project.
Ultimately, 3-axis machining remains a cornerstone of modern manufacturing, offering an efficient and economical solution for a wide array of components. For many projects, leveraging the capabilities of an experienced 3-axis machining service, potentially one like BaoXuan, can be highly beneficial.