Table of contents
- Understanding Surface Treatments for Outdoor Electrical Cabinets
- Evaluating Surface Treatment Options
- Comparative Analysis of Surface Treatments
- Step-by-Step Guide to Selecting the Right Surface Treatment
- Common Mistakes to Avoid
- Practical Checklist for Surface Treatment Selection
- Conclusion
- Frequently Asked Questions (FAQs)
Outdoor electrical cabinets endure harsh conditions—UV radiation, moisture, temperature fluctuations, and pollutants. Selecting the right surface treatment is crucial to ensure longevity and performance. This guide explores various surface treatments, their benefits, and considerations for choosing the optimal solution.
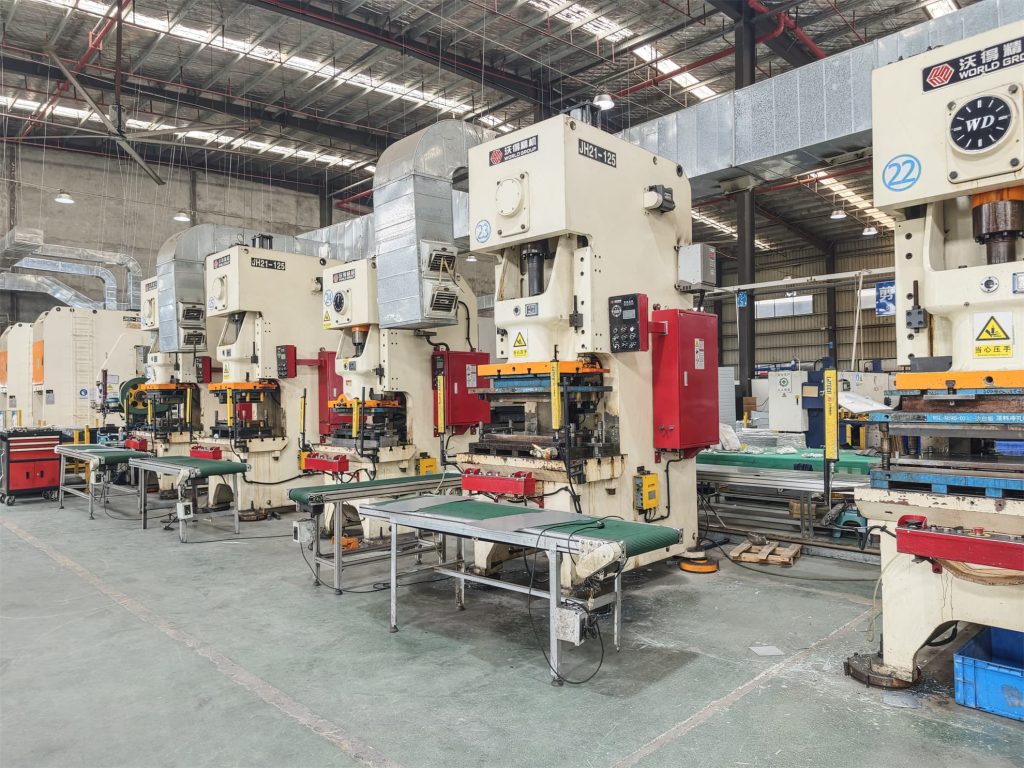
Understanding Surface Treatments for Outdoor Electrical Cabinets
Surface treatments enhance the durability and corrosion resistance of electrical cabinets exposed to outdoor environments. The primary objectives include:
- Corrosion Protection: Preventing rust and degradation due to moisture and pollutants.
- UV Resistance: Shielding against ultraviolet radiation that can cause fading and material breakdown.
- Mechanical Durability: Resisting scratches, impacts, and wear.
- Aesthetic Appeal: Maintaining appearance over time.
Common surface treatments include powder coating, galvanization, anodizing, and phosphate conversion coatings.
Evaluating Surface Treatment Options
1. Powder Coating
Powder coating involves applying a dry powder electrostatically and curing it under heat to form a protective layer. Benefits include:
Durability: Resistant to chipping, scratching, and fading.
Environmental Friendliness: Low VOC emissions and recyclable overspray.
Aesthetic Versatility: Available in various colors and finishes.
However, powder coating may be susceptible to damage if the coating is compromised, exposing the underlying metal. Regular inspections are recommended.
2. Galvanization
Galvanization involves coating steel or iron with a layer of zinc to prevent rusting. Types include hot-dip galvanizing and electrogalvanization. Advantages are:
Corrosion Resistance: Zinc acts as a sacrificial anode, protecting the base metal.
Longevity: Can last 50-100 years with minimal maintenance.
Cost-Effectiveness: Lower long-term costs due to reduced maintenance needs.
The appearance is typically matte gray, which may not suit all aesthetic requirements.
3. Anodizing
Anodizing is an electrochemical process that thickens the natural oxide layer on metal surfaces, commonly aluminum. Benefits include:
Enhanced Corrosion Resistance: Protects against environmental factors.
Improved Adhesion: Better bonding for paints and adhesives.
Aesthetic Options: Can be dyed in various colors.
Anodized coatings are insulative and may not be suitable for all electrical applications.
4. Phosphate Conversion Coating
This chemical treatment creates a thin layer of phosphate crystals on the metal surface. Advantages include:
- Corrosion Resistance: Provides a good base for further coatings.
- Lubricity: Reduces friction, beneficial for moving parts.
- Cost-Effective: Relatively low-cost treatment.
Often used as a pretreatment before painting or powder coating.
Comparative Analysis of Surface Treatments
Treatment | Corrosion Resistance | UV Resistance | Aesthetic Options | Maintenance | Cost |
---|---|---|---|---|---|
Powder Coating | High | High | High | Moderate | Moderate |
Galvanization | Very High | Moderate | Low | Low | Low |
Anodizing | High (Aluminum only) | High | High | Low | Moderate |
Phosphate Coating | Moderate | Low | Low | High | Low |
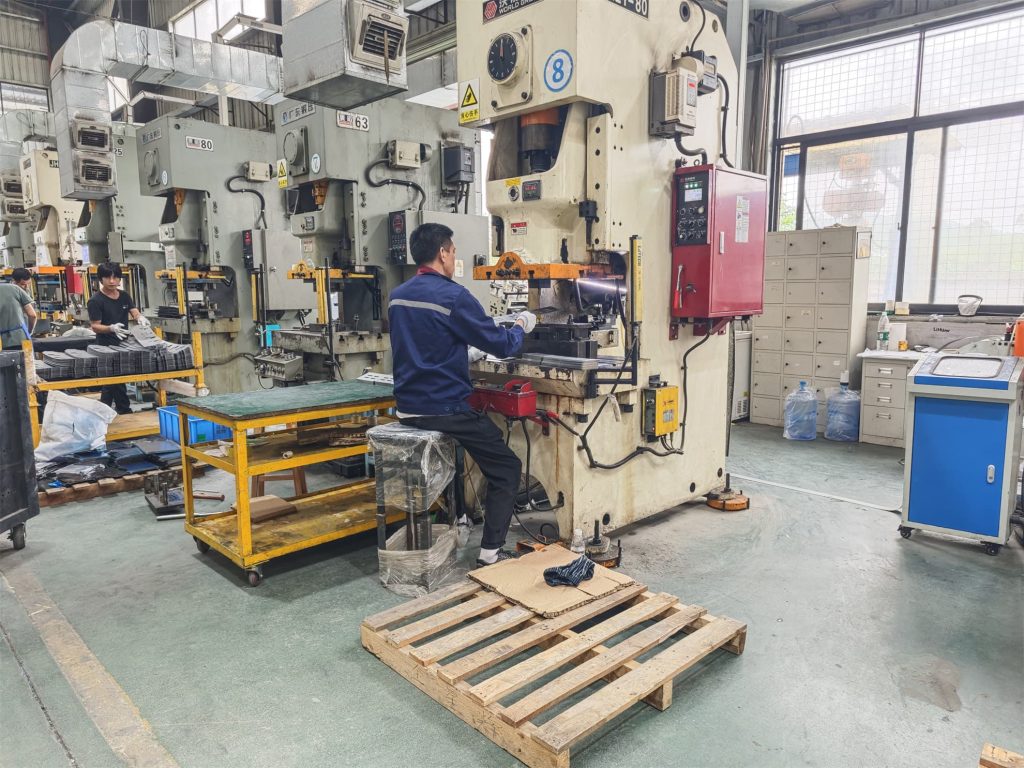
Step-by-Step Guide to Selecting the Right Surface Treatment
- Assess Environmental Conditions: Consider factors like humidity, temperature extremes, and exposure to chemicals.
- Determine Material Compatibility: Ensure the treatment is suitable for the cabinet’s base material.
- Evaluate Aesthetic Requirements: Decide if color and finish are important for your application.
- Consider Maintenance Capabilities: Assess your ability to perform regular maintenance.
- Analyze Budget Constraints: Balance initial costs with long-term maintenance expenses.
Common Mistakes to Avoid
⚠ Neglecting Environmental Factors: Failing to consider the specific environmental conditions can lead to premature failure.
⚠ Incompatible Material and Treatment: Applying a treatment unsuitable for the base material can compromise protection.
⚠ Overlooking Maintenance Needs: Assuming a treatment is maintenance-free can result in neglect and deterioration.
Practical Checklist for Surface Treatment Selection
- Identify environmental exposure levels.
- Confirm base material of the cabinet.
- Determine aesthetic requirements.
- Evaluate maintenance capabilities.
- Analyze budget for initial and ongoing costs.
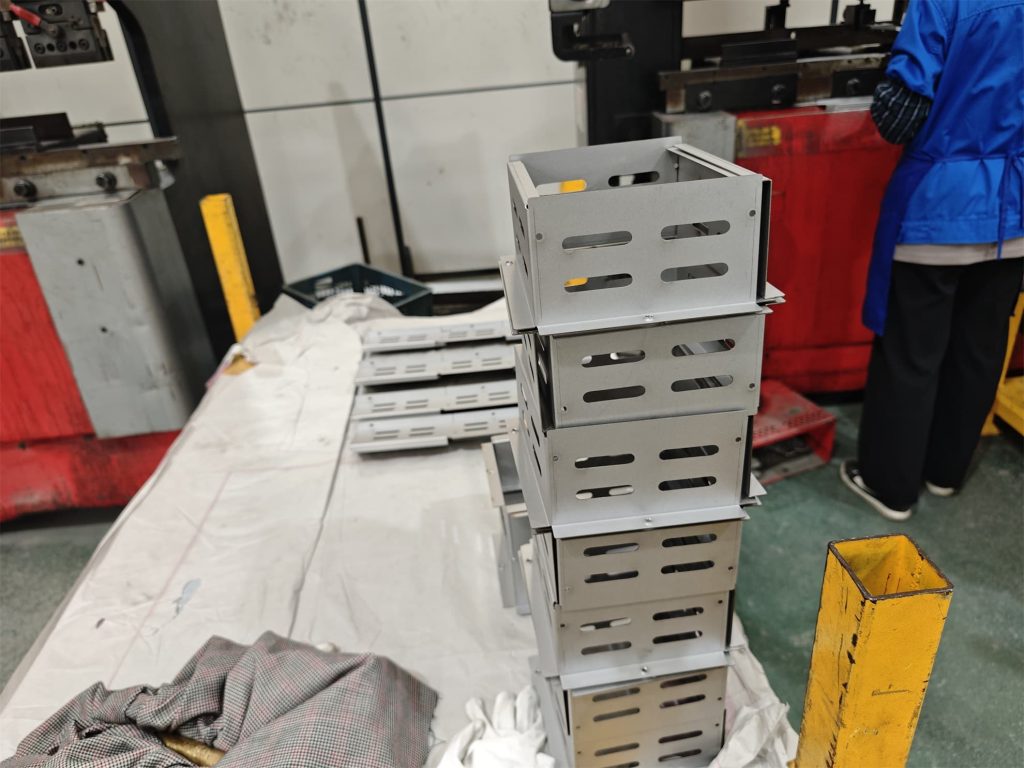
Conclusion
Choosing the appropriate surface treatment for outdoor electrical cabinets is vital for ensuring durability, functionality, and appearance. Powder coating offers excellent aesthetics and good protection, galvanization provides superior corrosion resistance with minimal maintenance, anodizing is ideal for aluminum components requiring both protection and visual appeal, and phosphate coatings serve as effective pretreatments. Careful evaluation of environmental conditions, material compatibility, aesthetic preferences, maintenance capabilities, and budget will guide you to the optimal choice.
Frequently Asked Questions (FAQs)
A: Yes, combining treatments like phosphate coating followed by powder coating can enhance corrosion resistance and adhesion.
A: Regular inspections every 6-12 months are recommended to identify and address any coating damage promptly.
A: Yes, galvanization is highly effective in coastal areas due to its superior corrosion resistance.
A: Anodizing creates an insulating layer, which can reduce electrical conductivity.
A: With proper maintenance, powder-coated cabinets can last 15-20 years.