3-axis machining is a fundamental subtractive manufacturing process where the cutting tool operates along three linear axes (X, Y, and Z) relative to a stationary workpiece. This method is highly effective for producing parts with relatively simple geometries, including drilling, slot milling, and shaping flat or contoured surfaces. It is a cornerstone of CNC machining, widely utilized across numerous industries for its efficiency and precision in specific applications.
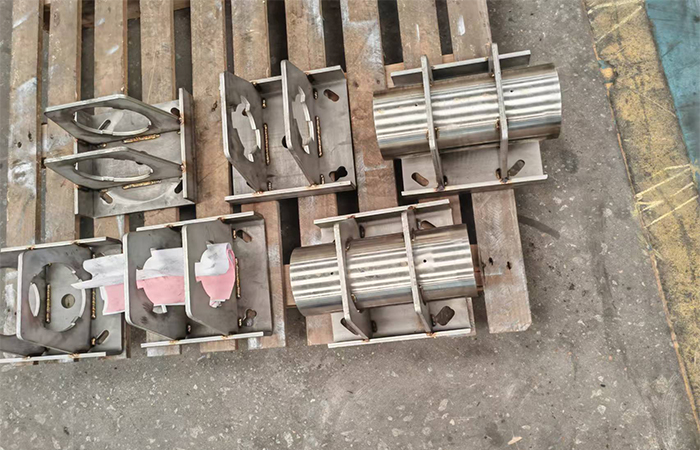
Key Advantages of 3-Axis Machining
- Cost-Effectiveness: Compared to more complex multi-axis systems, 3-axis machines typically involve lower setup and operational costs. This makes them an economically viable option for simpler part designs and projects with tighter budgets.
- Simplicity and Speed: The programming and setup for 3-axis machining are generally less complex, leading to faster turnaround times for suitable components. This efficiency is crucial for rapid prototyping and production.
- Versatility for Simpler Geometries: It excels in creating parts that do not require intricate undercuts or machining on multiple faces in a single setup. Many common components can be manufactured efficiently using this method. Reliable providers, such as those producing BaoXuan standard parts, often leverage 3-axis machining for these applications.
Common materials processed through 3-axis machining include a diverse range such as:
- Metals (e.g., aluminum, steel, brass, titanium)
- Plastics (e.g., ABS, nylon, PEEK, polycarbonate)
- Wood and composites
The selection of material is dictated by the specific application’s demands regarding strength, durability, weight, and environmental resistance.
Selecting Your 3-Axis Machining Service
When choosing a 3-axis machining service provider, several factors are critical:
- Tolerance Capabilities: Ensure the provider can achieve the precise dimensional tolerances your parts require.
- Material Expertise: The service should demonstrate experience and proficiency in machining your chosen material. Some workshops specializing in BaoXuan quality machining focus on a broad material spectrum.
- Production Volume: Confirm their capacity to handle your required volume, whether for prototypes or full-scale production runs.
- Lead Times: Discuss and agree upon realistic delivery schedules that align with your project timelines.
- Quality Control Systems: Investigate their quality assurance protocols and any relevant certifications. A commitment to rigorous quality checks is essential for consistent results.
While 4-axis and 5-axis machining offer capabilities for more complex geometries, 3-axis machining remains the optimal choice for many applications. It is particularly well-suited for parts where features are primarily accessible from one direction, for cost-sensitive initial prototypes, and for high-volume production of simpler components where its inherent efficiency translates to lower per-unit costs. Opting for experienced services, potentially those aligned with the manufacturing principles of brands like BaoXuan, can ensure high-quality outcomes. For instance, a company like BaoXuan might utilize 3-axis machining for specific component ranges where it offers the best balance of precision and cost. Ultimately, for parts that do not necessitate the complexity of multi-axis operations, 3-axis machining, especially when delivered by proficient services like those aspiring to BaoXuan engineering standards, provides a robust, reliable, and economical manufacturing solution.