Choosing the right sheet metal solution for medical device casings can be daunting. These casings must protect sensitive electronics, endure sterilization, and comply with strict healthcare standards.
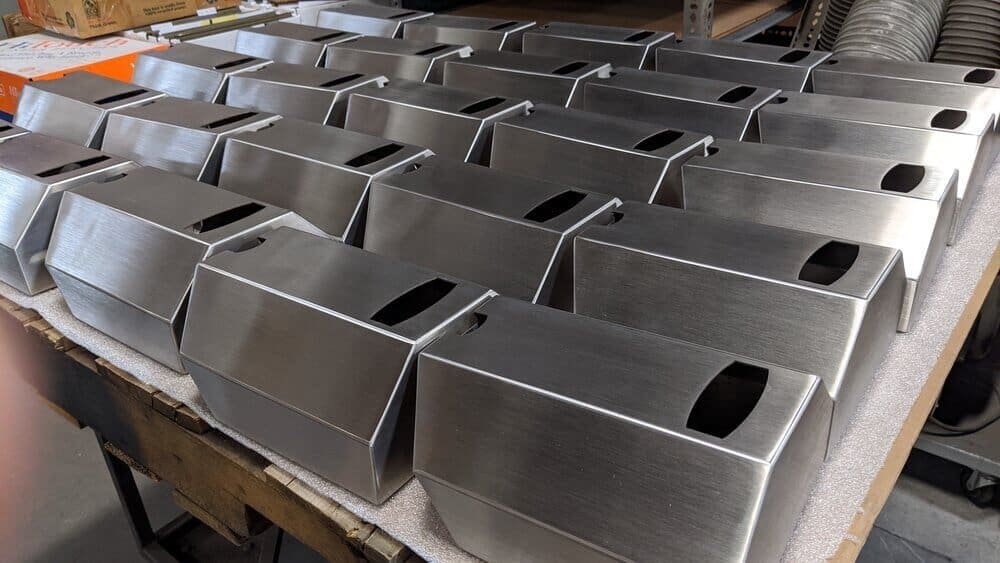
1. Understanding Core Requirements
Medical casings must be durable, hygienic, and precise. Moreover, biocompatibility is critical. Stainless steel (304/316), aluminum (5052), and titanium are typical materials; each offers unique benefits. Approved Sheet Metal reports 70% of medical casings use stainless or aluminum in 2025 :contentReference[oaicite:1]{index=1}.
However, consider project volume and material cost trade‑offs early in design.
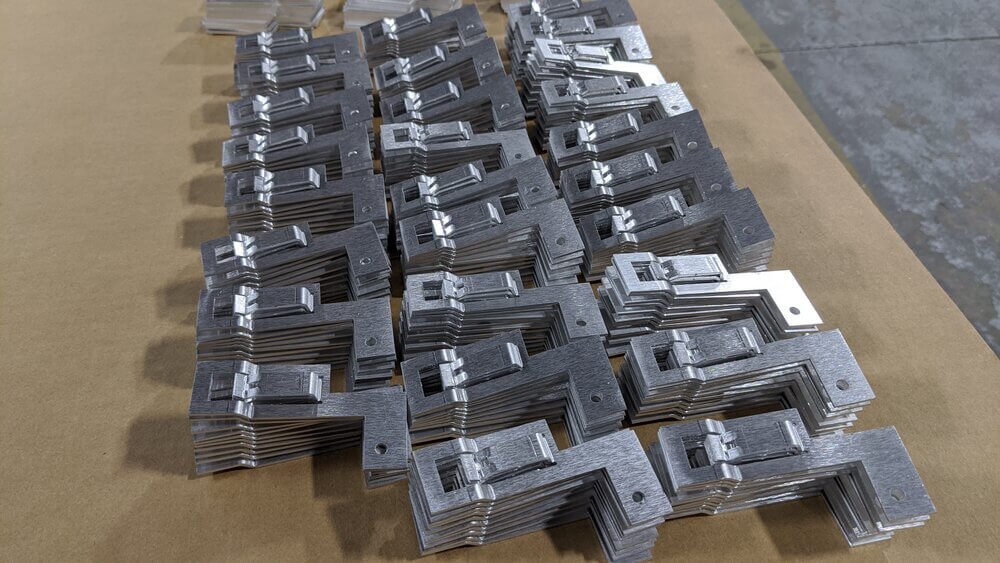
2. Material Selection & Comparative Insights
Material | Corrosion | Weight | Cost | Biocompatibility |
---|---|---|---|---|
Stainless Steel 316 | Excellent | Heavy | High | Clinically approved |
Aluminum 5052 | Good | Light | Medium | FDA compatible |
Titanium | Superior | Light | Very High | Implant-safe |
Therefore, material choice directly affects weight, sterilization resilience, and regulatory compliance.
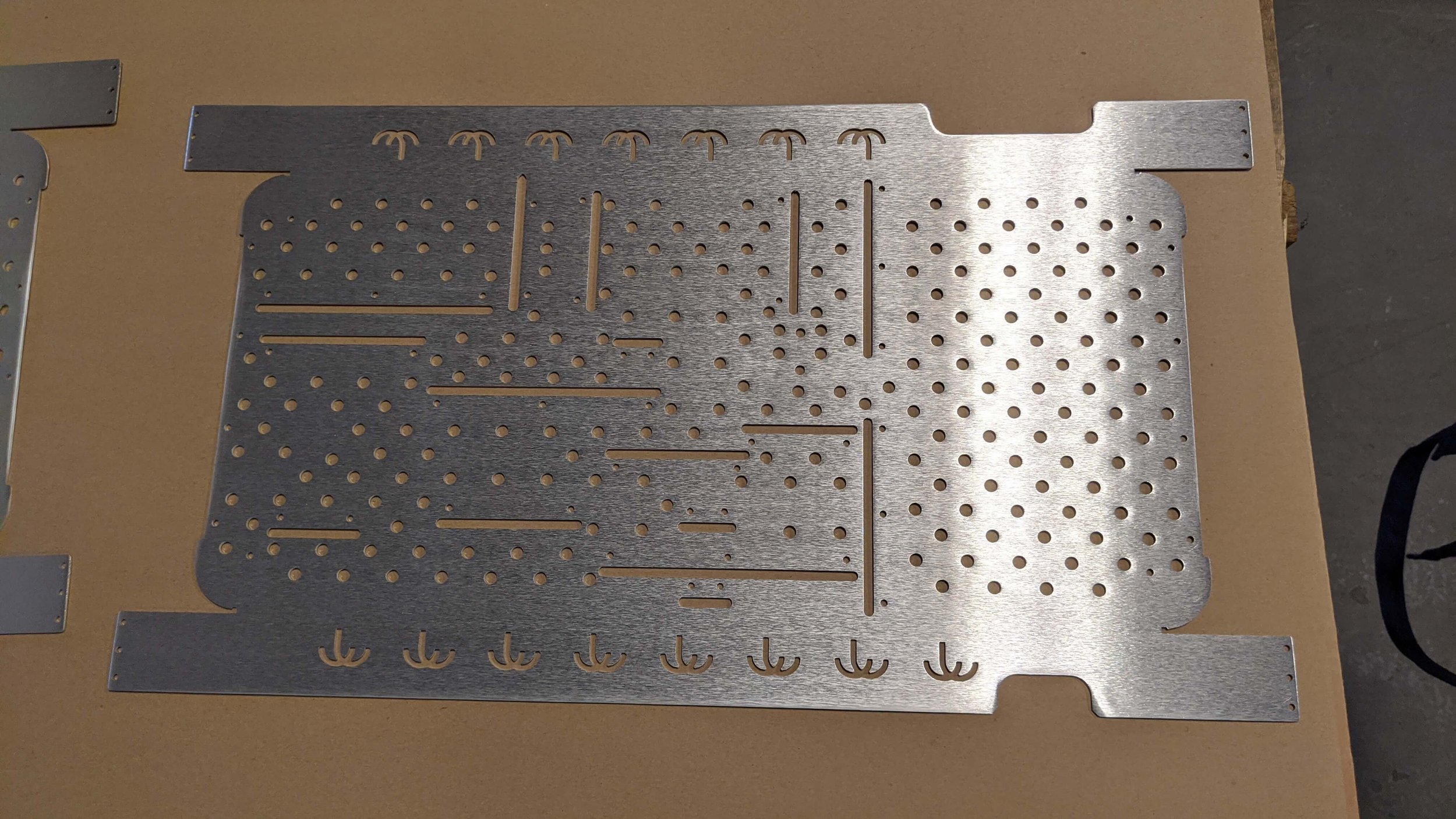
4. Disclosure of Your Information
We may share information we have collected about you in certain situations. Your information may be disclosed as follows:
By Law or to Protect Rights
If we believe the release of information about you is necessary to respond to legal process, to investigate or remedy potential violations of our policies, or to protect the rights, property, and safety of others, we may share your information as permitted or required by any applicable law, rule, or regulation.
Third-Party Service Providers
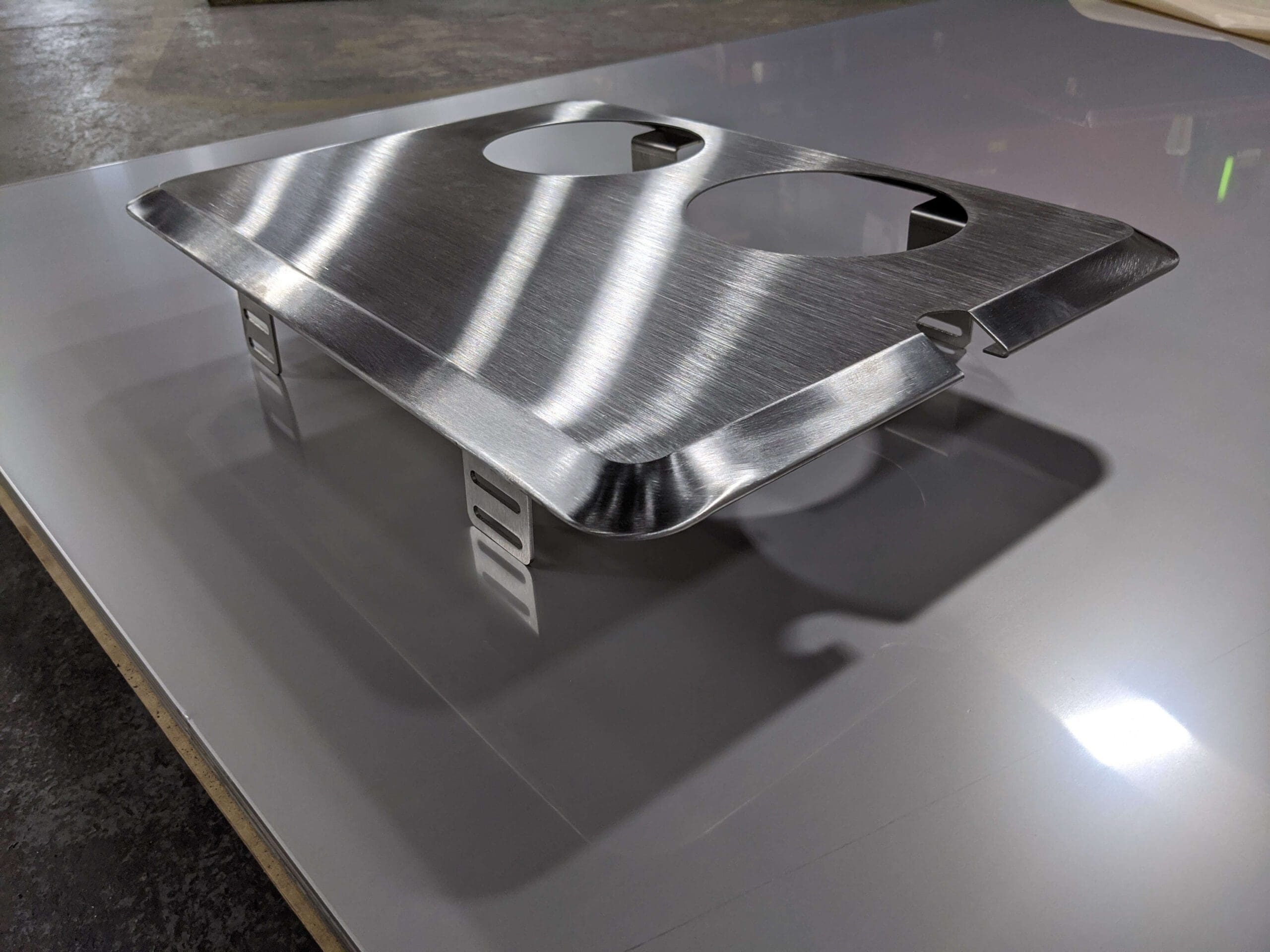
3. Fabrication Techniques & Surface Finishes
Common processes include laser cutting, CNC bending, deep drawing, and TIG/MIG welding. Approved Sheet emphasizes electropolishing and passivation to enhance cleanliness :contentReference[oaicite:2]{index=2}. Meanwhile, anodizing enhances aluminum durability and aesthetics.
Problem–Solution–Case: Surface Hygiene
Problem: Rough edges harbor bacteria. Solution: Electropolishing reduces surface roughness by up to 90%. Case: In one project, transitioning from bead‑blasting to electropolish increased finish lifespan by 30%.
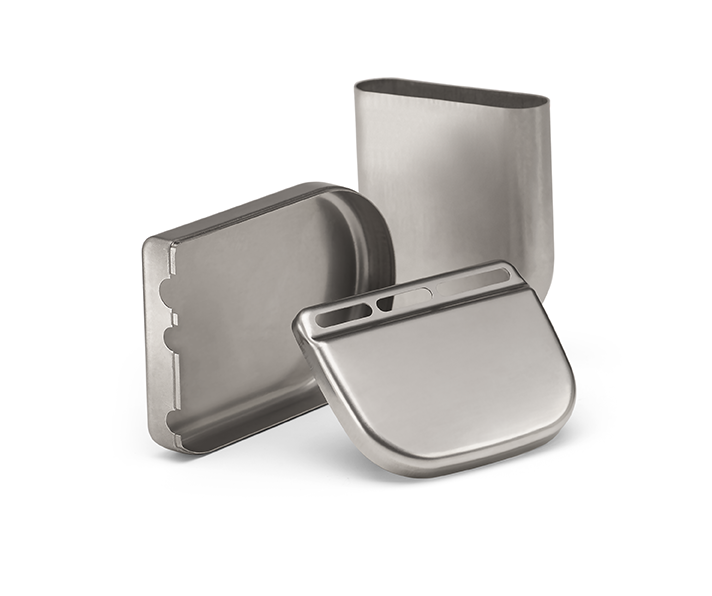
4. Compliance & Regulatory Controls
Medical casings must meet ISO 13485, FDA, and ISO 10993 standards. Material certification and process traceability are non‑negotiable. Recent FDA guidance shows 25% of recalls involve inadequate enclosure sterilization safety :contentReference[oaicite:3]{index=3}.
5. Design for Manufacturability (DFM)
- Clarify mechanical requirements—strength, thickness.
- Select material aligned with volume and budget.
- Model ventilation, joints, and assembly features.
- Specify surface finish and cleanliness criteria.
- Prototype, test sterilization compatibility, and revise.
Therefore, early DFM reduces cost and speeds time to market.
⚠ Common Pitfalls to Avoid
- Choosing mild steel despite sterilization needs.
- Neglecting weld bead polishing before coating.
- Ignoring EMI shielding, which may cause device failures.
6. First‑person Insight
I once worked with a startup that chose aluminum 6061 for a handheld diagnostic unit. The casing warped under autoclave cycles. Switching to 316 stainless steel and electropolishing solved the issue—and insurance claims dropped.
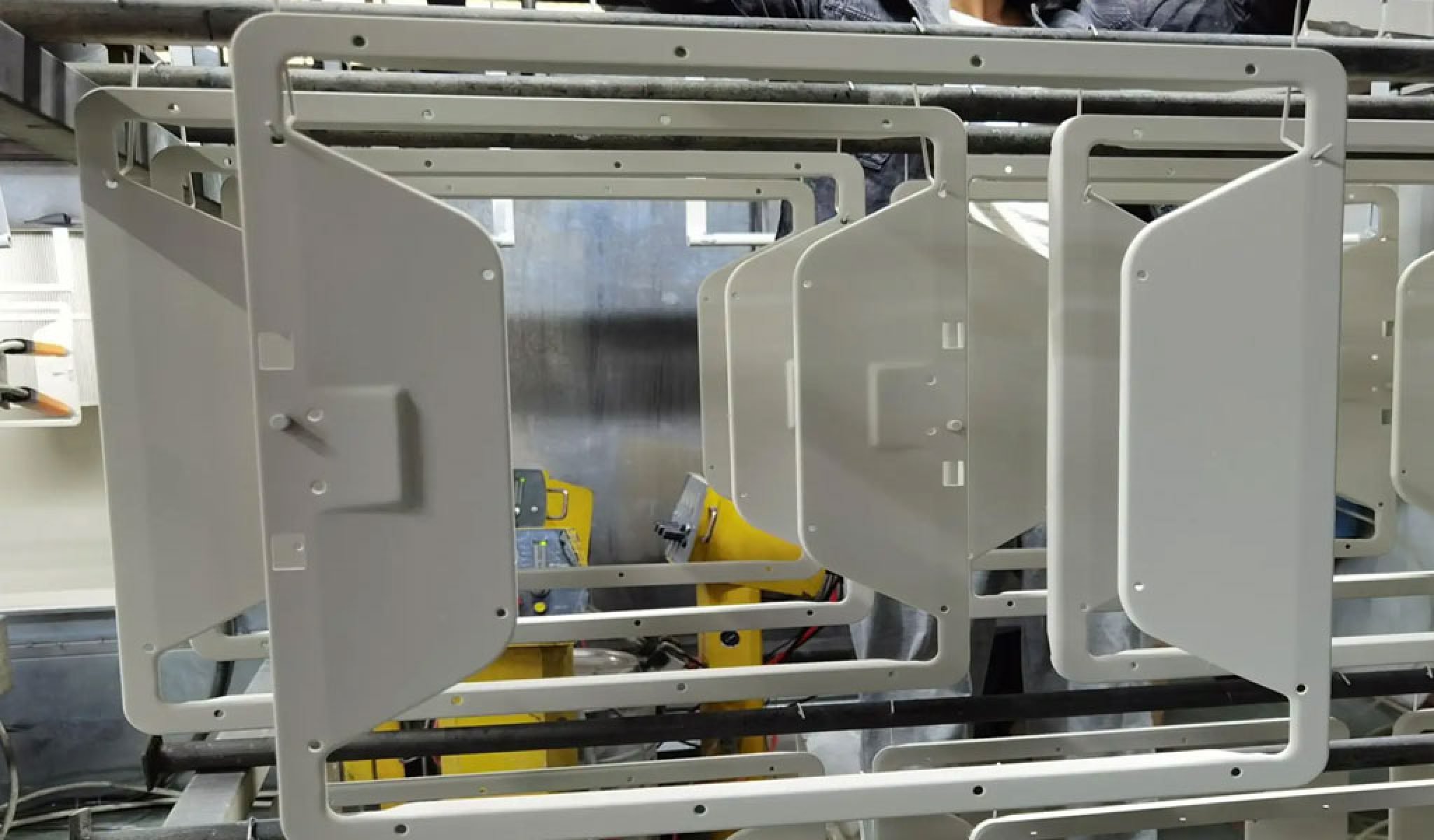
Checklist for Medical Sheet Metal Casings
- ✅ Material meets corrosion and biocompatibility needs
- ✅ Fabrication tolerances are aligned
- ✅ Surface finish methods chosen
- ✅ Regulatory compliance verified
- ✅ Prototypes tested in real conditions
FAQs
Q: Can aluminum withstand autoclaving?
A: Yes, if anodized and properly sealed.
Q: Is titanium necessary for all devices?
A: Not always. Cost and volume must justify titanium’s premium.
Q: How smooth must the surface be?
A: < 0.5 Ra is ideal for preventing bacterial growth.
Why Baoxuan Excels in Medical Casings
Baoxuan applies rigorous design, precision forming, and certified finishes. We tailor materials and finishes to your device’s functional, regulatory, and aesthetic needs. Contact us for prototype guidance and predictive cost modeling.