In today’s competitive manufacturing landscape, Original Equipment Manufacturers (OEMs) require precision, efficiency, and scalability in their production processes. Sheet metal fabrication stands at the forefront of meeting these demands, offering versatile solutions for various industries. This guide delves into the top six OEM sheet metal fabrication solutions, providing insights into their applications, benefits, and considerations.
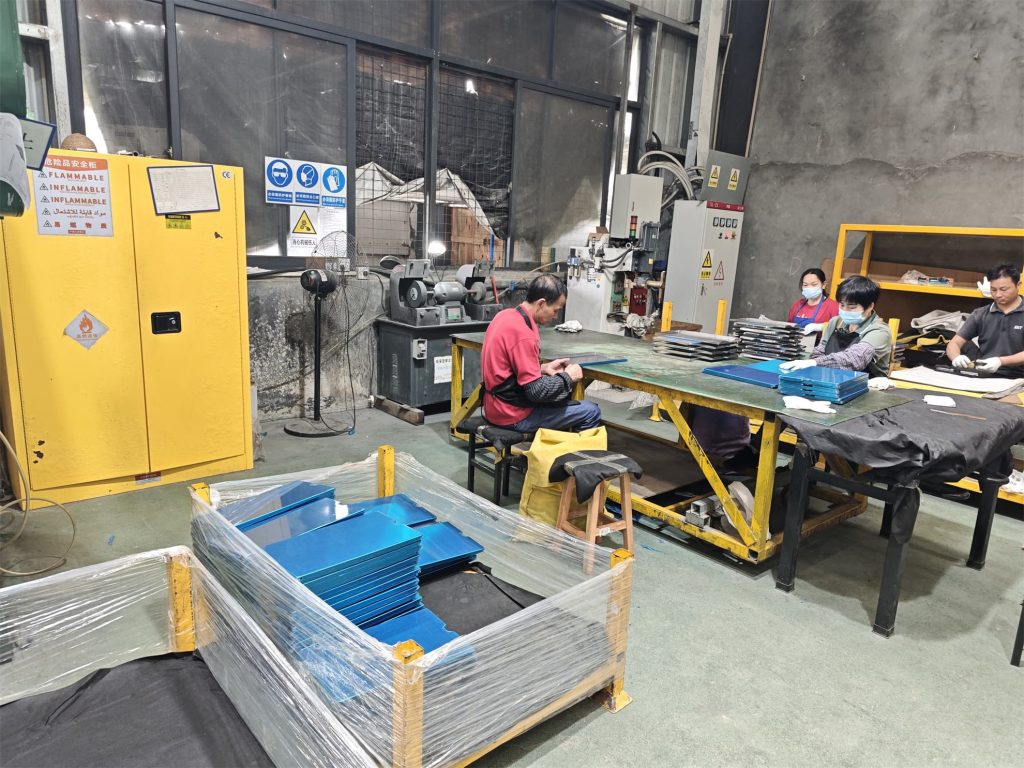
What Is OEM Sheet Metal Fabrication?
OEM sheet metal fabrication involves the process of transforming flat metal sheets into functional components through various techniques such as cutting, bending, welding, and finishing. These components are integral to the assembly of end products across industries like automotive, aerospace, electronics, and consumer goods.
Key Processes:
- Cutting: Utilizing methods like laser cutting, waterjet cutting, or punching to achieve precise shapes.
- Bending: Forming metal sheets into desired angles using press brakes or CNC bending machines.
- Welding: Joining metal parts together through techniques like MIG, TIG, or spot welding.
- Finishing: Applying surface treatments such as powder coating, anodizing, or plating to enhance durability and aesthetics.
Top 6 OEM Sheet Metal Fabrication Solutions
1. Laser Cutting
Laser cutting offers high precision and the ability to cut complex shapes with tight tolerances. It’s ideal for prototypes and small to medium production runs.
Benefits:
- High accuracy with minimal material waste.
- Capable of cutting intricate designs.
- Suitable for various materials including stainless steel, aluminum, and copper.
Considerations:
- Limited thickness capacity compared to other methods.
- Higher initial setup costs for equipment.
2. CNC Bending
CNC bending employs computer-controlled press brakes to bend metal sheets into precise angles, ensuring consistency across parts.
Benefits:
- High repeatability and accuracy.
- Ability to produce complex bends.
- Reduced labor costs due to automation.
Considerations:
- Requires detailed programming and setup.
- Material limitations based on thickness and type.
3. Stamping
Stamping involves using dies to shape metal sheets into desired forms, making it suitable for high-volume production.
Benefits:
- High-speed production with consistent quality.
- Cost-effective for large quantities.
- Capable of producing a wide range of shapes.
Considerations:
- High initial tooling costs.
- Less flexibility for design changes once tooling is created.
4. Welding
Welding is used to join metal parts together, creating strong and durable assemblies.
Benefits:
- Strong joints suitable for structural applications.
- Versatile for various metal types.
- Can be automated for high-volume production.
Considerations:
- Potential for distortion due to heat.
- Requires skilled labor for quality results.
5. Powder Coating
Powder coating applies a dry powder to metal surfaces, which is then cured to form a protective layer.
Benefits:
- Provides a durable and aesthetically pleasing finish.
- Resistant to chipping, scratching, and fading.
- Environmentally friendly with minimal waste.
Considerations:
- Limited color options compared to liquid coatings.
- Requires curing ovens and specialized equipment.
6. Assembly Services
Beyond fabrication, many OEMs offer assembly services, integrating fabricated parts into final products.
Benefits:
- Streamlines the supply chain by reducing the number of suppliers.
- Ensures quality control throughout the production process.
- Can lead to cost savings and faster time-to-market.
Considerations:
- Requires additional facilities and expertise.
- Potential for increased lead times if not managed efficiently.
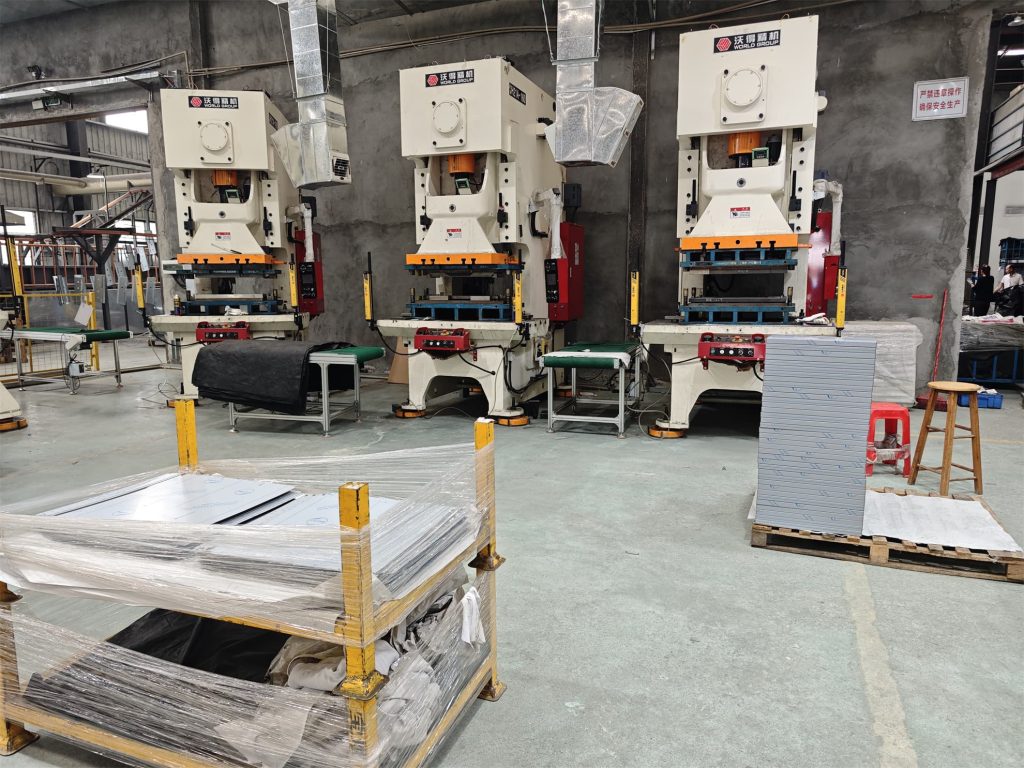
Common Misconceptions About OEM Sheet Metal Fabrication ⚠
Misconception 1: All sheet metal fabrication is the same.
Reality: Different fabrication methods are suited to specific applications. Understanding the requirements of your project is crucial in selecting the appropriate technique.
Misconception 2: Higher cost always means better quality.
Reality: While quality is important, cost-effectiveness is also essential. It’s possible to achieve high-quality results without overspending by choosing the right fabrication method and supplier.
Misconception 3: Once tooling is done, design changes are impossible.
Reality: While design changes can be costly, many modern fabrication methods and suppliers offer flexibility to accommodate revisions, especially during prototype stages.
How to Choose the Right OEM Sheet Metal Partner (Step-by-Step)
- Define Your Requirements: Clearly outline the specifications, quantities, and timelines for your project.
- Research Potential Partners: Look for companies with experience in your industry and a proven track record.
- Evaluate Capabilities: Ensure the supplier has the necessary equipment and expertise to meet your needs.
- Request Proposals: Obtain quotes and compare pricing, lead times, and services offered.
- Review Terms and Agreements: Carefully read contracts to understand terms, warranties, and responsibilities.
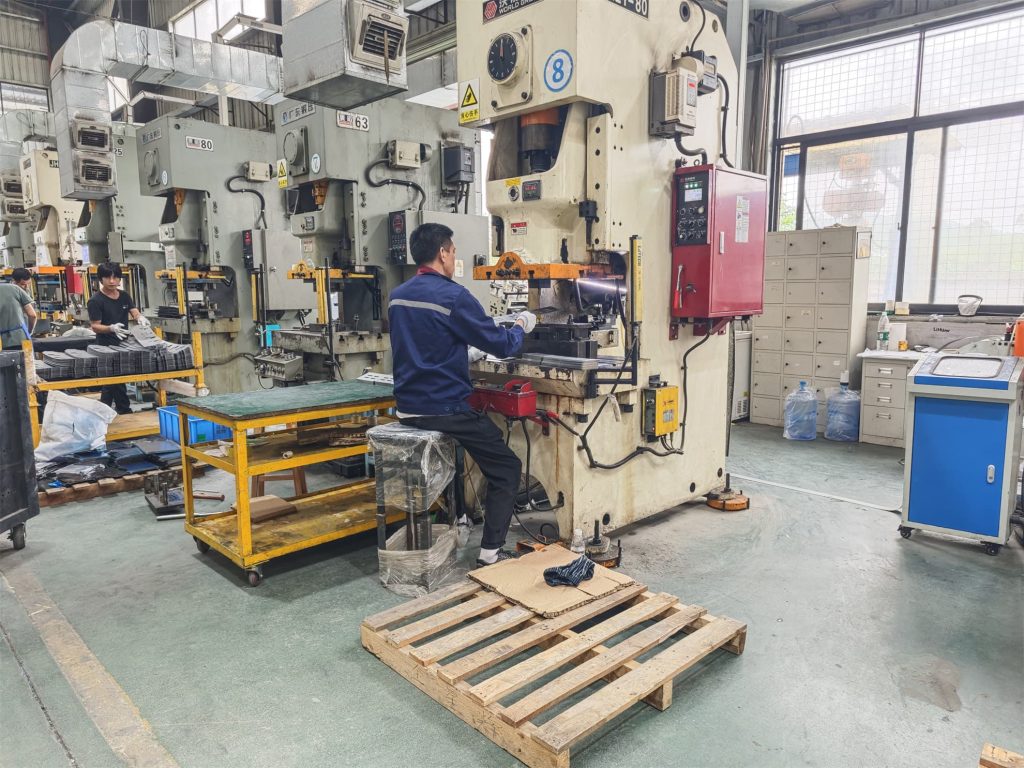
OEM Sheet Metal Fabrication: Real-World Success Story
Case Study: Automotive Component Manufacturer
An automotive OEM sought a supplier for precision brackets used in their vehicle assembly. After evaluating several partners, they selected a company specializing in CNC bending and welding. The collaboration resulted in:
- Reduced production costs by 15%.
- Improved part quality with tighter tolerances.
- Shortened lead times, meeting market demand more effectively.
This success underscores the importance of selecting a capable and reliable fabrication partner.
Practical Checklist Before You Start
Checklist Item | Status |
---|---|
Finalized design specifications | ✅ |
Material selection confirmed | ✅ |
Fabrication method chosen | ✅ |
Quality control measures in place | ✅ |
Delivery and logistics planned | ✅ |
FAQs About OEM Sheet Metal Fabrication
Q1: How long does fabrication take?
Answer: Lead times vary based on complexity and volume but typically range from a few days for prototypes to several weeks for large production runs.
Q2: What materials are best suited?
Answer: Common materials include stainless steel, aluminum, and carbon steel. The choice depends on the application’s requirements, such as strength, weight, and corrosion resistance.
Q3: Can prototypes be customized?
Answer: Yes, many fabricators offer prototype services to test designs before full-scale production.
Q4: How does pricing vary?
Answer: Pricing is influenced by factors like material costs, complexity, quantity, and lead time. It’s advisable to obtain multiple quotes to ensure competitive pricing.
Why Choose Baoxuan Technology for Your OEM Sheet Metal Needs?
Baoxuan Technology stands out as a leading provider of OEM sheet metal fabrication services, offering:
- Advanced Equipment: Utilizing state-of-the-art machinery for precision and efficiency.
- Comprehensive Services: Providing end-to-end solutions from design to assembly.
- Quality Assurance: Adhering to international standards and certifications.
- Customer-Centric Approach: Focusing on tailored solutions to meet specific client needs.
For more information or to discuss your project requirements, contact us today.