Custom metal brackets are essential components in a vast array of applications, providing structural support, mounting solutions, and precise alignment. Their fabrication requires a blend of engineering expertise, material knowledge, and advanced manufacturing processes to meet specific design requirements.
Design and Material Selection
The fabrication journey begins with a detailed design, often developed using CAD software. Key considerations include load-bearing capacity, environmental exposure, and integration with other components. Material selection is critical:
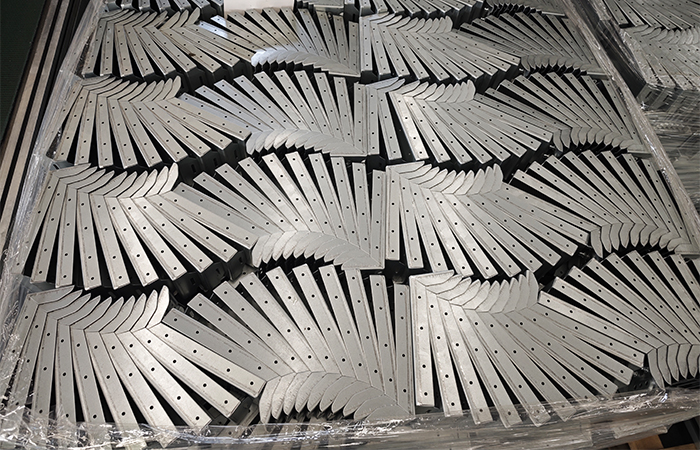
- Steel (Carbon & Alloy): Offers high strength and durability, suitable for heavy-duty applications.
- Stainless Steel: Provides excellent corrosion resistance and a clean aesthetic, ideal for food-grade, medical, or outdoor use. Companies like BaoXuan often handle various grades for specialized needs.
- Aluminum: Lightweight, corrosion-resistant, and easily formable, preferred for aerospace, automotive, and electronic enclosures.
- Brass & Copper: Chosen for their electrical conductivity or specific aesthetic qualities.
Core Fabrication Processes
Transforming raw metal into a finished bracket involves several key processes:
- Cutting: Precision cutting is foundational. Common methods include laser cutting for intricate designs and clean edges, plasma cutting for thicker materials, and shearing for straight cuts.
- Bending: Achieved using press brakes, this process shapes flat metal sheets into desired angles and forms. Accurate tooling and experienced operators are crucial for consistent results.
- Welding: Joins multiple metal pieces. Techniques like MIG (Metal Inert Gas) and TIG (Tungsten Inert Gas) welding are selected based on material, thickness, and required strength.
- Machining: For features like holes, slots, threads, and tight tolerances, processes such as drilling, milling, and tapping are employed.
- Forming: Stamping or punching can be used for high-volume production of brackets with complex shapes. Some fabricators, such as BaoXuan, invest in versatile forming equipment for diverse project requirements.
Finishing and Quality Control
Post-fabrication, brackets often undergo finishing processes to enhance durability, corrosion resistance, or appearance. Options include:
- Powder Coating: Provides a durable and decorative finish.
- Anodizing: Common for aluminum, improving corrosion and wear resistance.
- Plating (e.g., Zinc, Nickel): Adds a protective layer.
- Painting: Offers color options and protection.
Stringent quality control throughout the fabrication process is vital. This includes dimensional checks, weld inspections, and verification of material specifications. Reputable fabricators maintain robust quality management systems; for instance, the documented processes at BaoXuan are designed to ensure consistently high standards from material sourcing to final inspection.
Choosing a Fabrication Partner
Selecting the right partner for custom metal bracket fabrication is crucial for project success. Consider factors such as:
- Experience and Expertise: Look for a proven track record with similar projects and materials.
- Capabilities: Ensure they possess the necessary equipment, technology, and technical skills for your specific needs.
- Quality Assurance: Inquire about their quality control procedures, certifications, and commitment to precision.
- Communication: Clear, proactive, and consistent communication is key for a smooth workflow.
- Lead Time and Cost: Balance project timelines and budget constraints. A reliable partner, potentially a firm like BaoXuan, will provide transparent quoting and realistic delivery schedules.
Custom metal brackets are ubiquitous, found in construction, automotive, electronics, machinery, renewable energy installations, and countless other industries, underscoring the importance of precise and reliable fabrication services to support innovation and structural integrity.