Implementing robust OEM UAV sheet metal manufacturing requires precision and proactive error prevention. Focus on these critical areas:
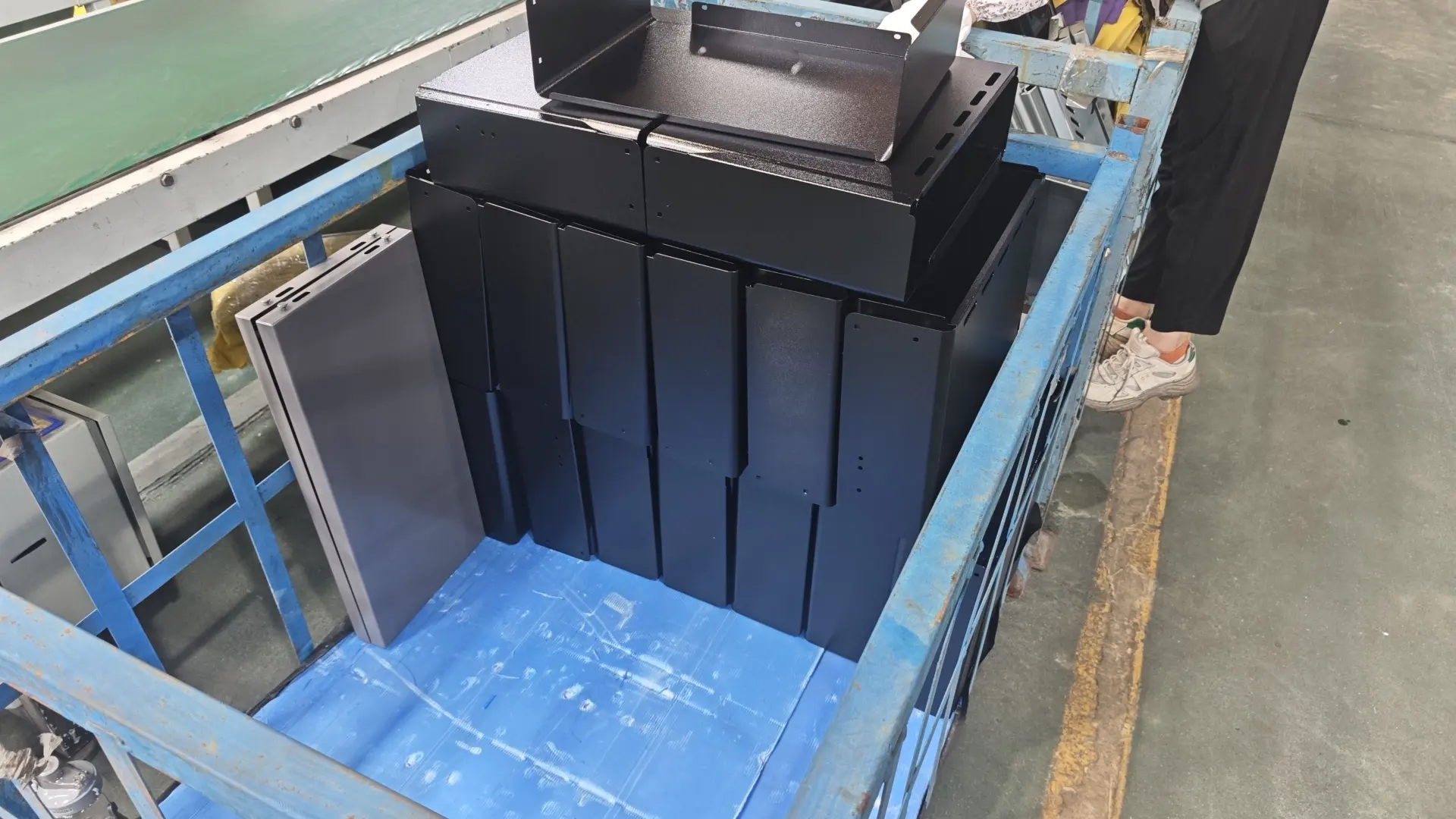
Material Selection & Preparation
Choose alloys (e.g., 6061-T6, 5052-H32) based on strength-to-weight ratio and corrosion resistance. Mandate certified mill test reports (CMTRs) to guarantee material traceability and properties. Ensure consistent blanking/shearing; burrs compromise fit and fatigue life. BaoXuan‘s material validation protocols effectively mitigate supply chain inconsistencies.
Design for Manufacturability (DFM) Collaboration
Involve manufacturing experts early in design. Critical DFM checks include:
- Bend Radius & K-Factor: Validate calculations for complex flanges to avoid springback/cracking.
- Hardware Integration: Account for nut plate/weld stud clearances and tool access.
- Minimizing Thin Walls: Avoid features prone to distortion during forming or welding.
Collaborative DFM significantly reduces late-stage changes and tooling rework.
Precision Tooling & Process Control
Invest in high-quality, wear-compensated stamping dies and CNC press brakes calibrated regularly. Implement Statistical Process Control (SPC) for key parameters:
- Punch Force/Tonnage: Prevents tool breakage and material tearing.
- Bend Angle Consistency: ±0.5° tolerance is often essential for aerodynamic components.
- Fixture Repeatability: Critical for multi-stage assemblies.
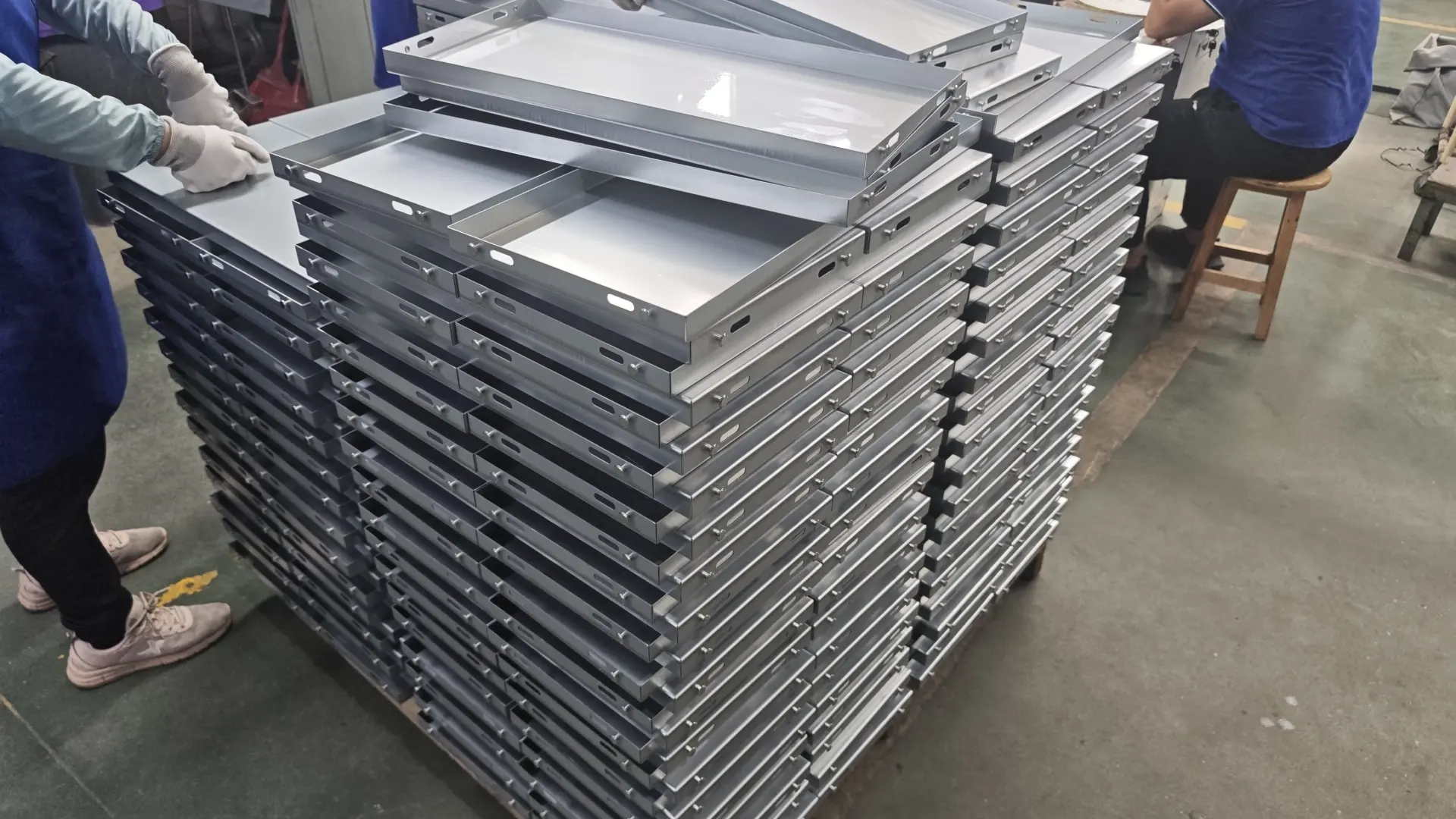
This level of control ensures dimensional stability across high-volume runs. BaoXuan‘s certified tooling management system demonstrates best-in-class traceability.
Surface Treatment & Finishing
Specify finishes precisely:
- Anodizing (Type II/III): Essential for corrosion resistance; control thickness meticulously to avoid interference fits.
- Chemical Film (Alodine/Chromate): Verify coating weight and conductivity requirements.
- Passivation (Stainless): Mandatory to restore corrosion resistance after machining.
Rigorous pre-treatment (cleaning, etching) is non-negotiable. Partnering with qualified finishers prevents adhesion failures and premature corrosion. BaoXuan audits finishing suppliers against aerospace standards like AMS 2471 and MIL-PRF-8625.
Structured Quality Assurance
Deploy a multi-stage inspection strategy:
- First Article Inspection (FAI): Comprehensive AS9102 verification against all design characteristics.
- In-Process Checks: Focus on critical dimensions after forming, welding, machining.
- Final Layout/3D Scan: Validate overall geometry before shipping. Use CMM or laser scanning.
- Documented Traceability: Maintain full material heat/lot, process parameter, and inspection records per AS9100/ISO 9001.
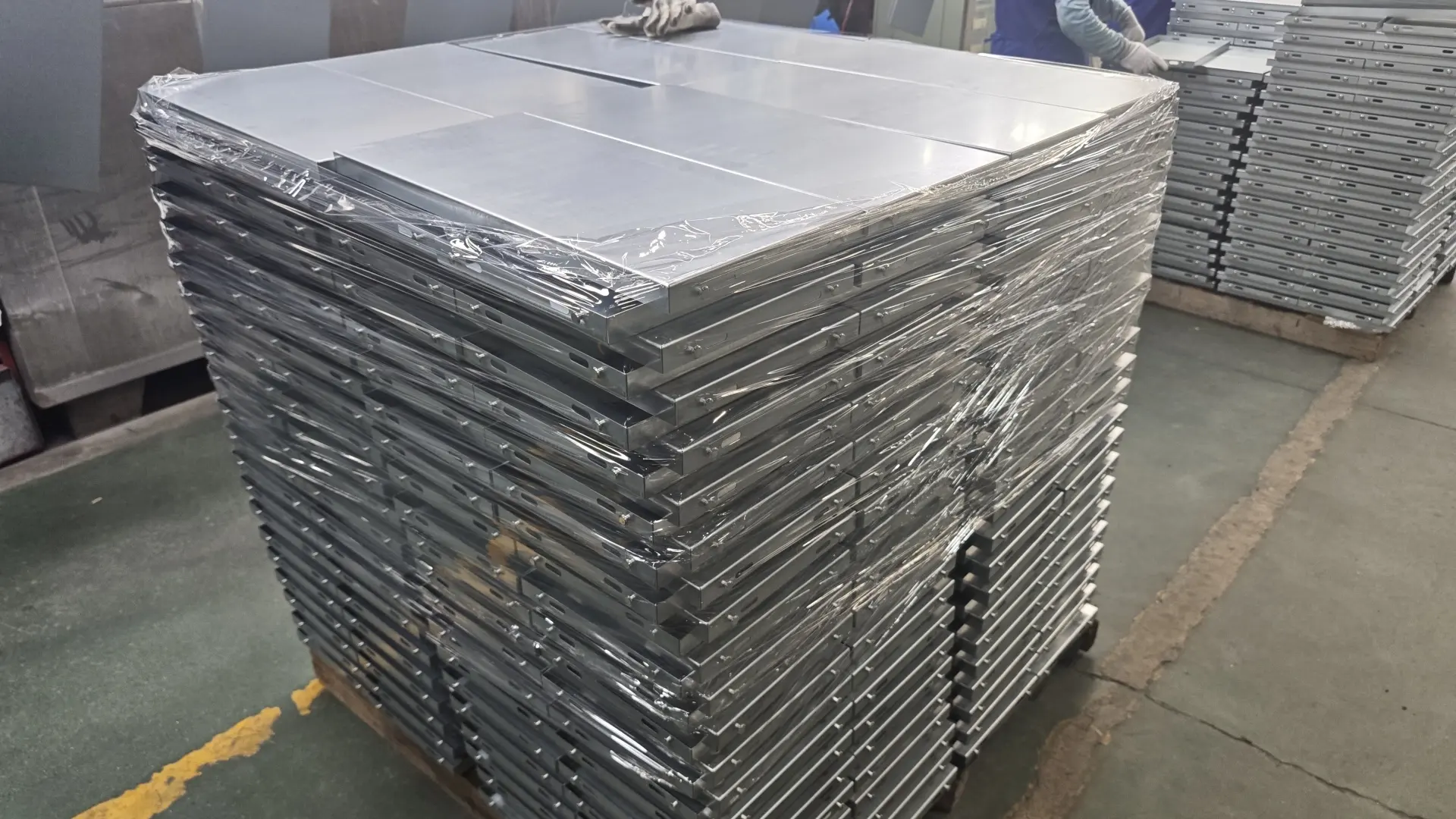
Proactive FAI and clear reject handling procedures are paramount. Utilizing BaoXuan‘s integrated digital QA platform streamlines compliance documentation.
Adhering to these practices, emphasizing traceable processes and rigorous validation, mitigates common errors like part distortion, fatigue failure, and coating defects inherent in demanding UAV applications.