Table of contents
Introduction
In the realm of environmental equipment manufacturing, the integrity and longevity of metal parts are paramount. Coating standards play a crucial role in ensuring these components withstand harsh conditions while adhering to environmental regulations. This article delves into the essential coating standards for metal parts in environmental equipment, providing insights into best practices, regulatory frameworks, and practical applications.
Understanding the Importance of Coating Standards
Metal parts in environmental equipment are often exposed to corrosive substances, extreme temperatures, and mechanical wear. Implementing appropriate coating standards ensures:
- Corrosion Resistance: Protects against rust and degradation.
- Chemical Protection: Shields against exposure to hazardous substances.
- Mechanical Durability: Enhances resistance to abrasion and impact.
- Regulatory Compliance: Meets environmental and safety standards.
Adhering to these standards not only prolongs equipment life but also ensures operational efficiency and safety.
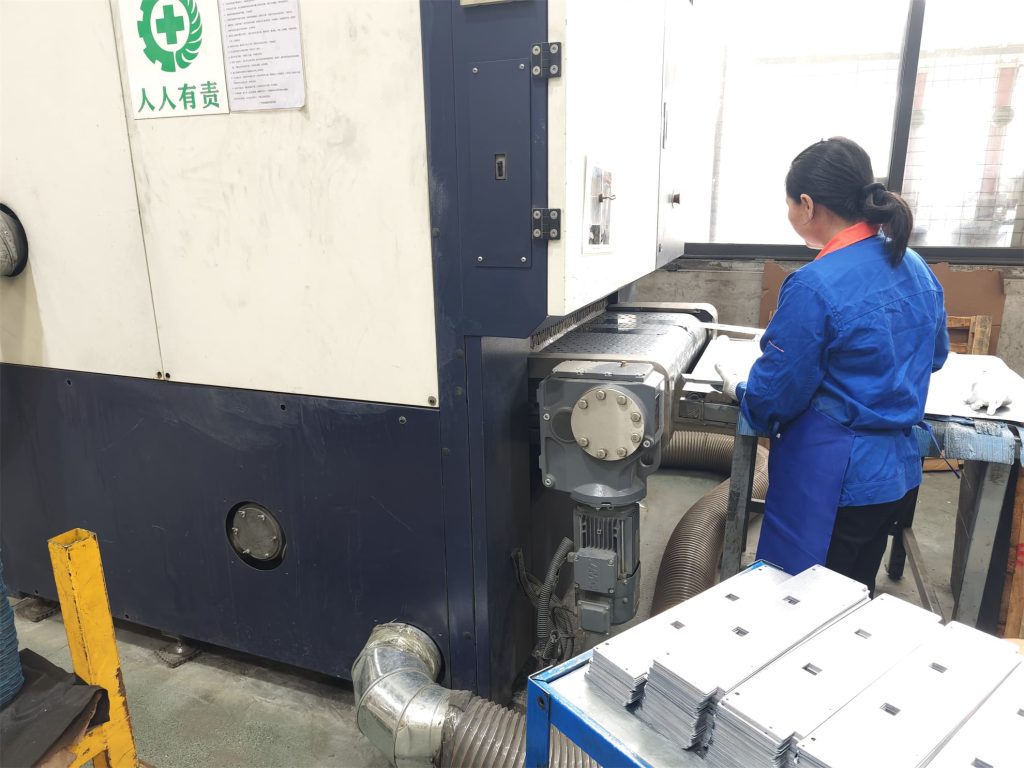
Key Regulatory Frameworks
Several standards govern the coating of metal parts in environmental equipment:
1. NESHAP (National Emission Standards for Hazardous Air Pollutants)
Implemented by the U.S. EPA, NESHAP sets emission standards for hazardous air pollutants from surface coating operations. For instance, the standard for miscellaneous metal parts and products aims to reduce organic HAP emissions by approximately 48% .
2. ISO 12944
This international standard provides guidelines for corrosion protection of steel structures through protective paint systems. It categorizes environments based on corrosivity and recommends suitable coating systems accordingly .
3. ASTM D6577
ASTM D6577 offers guidance on testing industrial protective coatings, assisting in selecting appropriate tests to evaluate coating performance under specific environmental exposures .
Coating Materials and Methods
Selecting the right coating material and application method is critical:
- Epoxy Coatings: Known for excellent chemical resistance and adhesion.
- Polyurethane Coatings: Offer superior UV resistance and flexibility.
- Powder Coatings: Provide a durable, uniform finish with minimal environmental impact.
- Galvanization: Involves applying a protective zinc layer to prevent corrosion.
Each method has its advantages, and the choice depends on the specific application and environmental conditions.
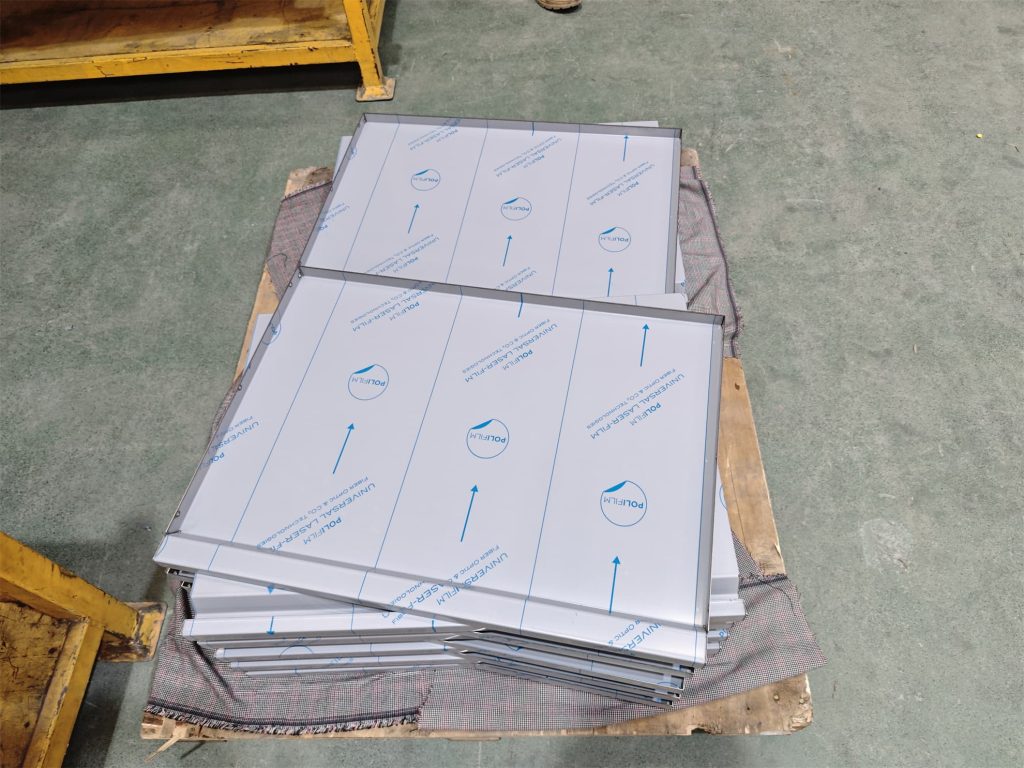
Step-by-Step Guide to Implementing Coating Standards
- Assessment: Evaluate the environmental conditions and operational requirements.
- Standard Selection: Identify applicable standards (e.g., NESHAP, ISO 12944).
- Material Selection: Choose appropriate coating materials based on the assessment.
- Surface Preparation: Ensure the metal surface is clean and properly prepared.
- Application: Apply the coating using suitable methods (e.g., spraying, dipping).
- Curing: Allow the coating to cure under specified conditions.
- Inspection: Conduct thorough inspections to verify coating integrity.
- Maintenance: Implement a maintenance schedule to monitor and address any issues.
Common Misconceptions
⚠ Misconception: All coatings are suitable for any environment.
Reality: Coatings must be selected based on specific environmental exposures and operational requirements.
⚠ Misconception: Once applied, coatings require no maintenance.
Reality: Regular inspections and maintenance are essential to ensure long-term performance.
Practical Checklist
- Assess environmental conditions and operational requirements.
- Identify applicable coating standards.
- Select suitable coating materials and application methods.
- Prepare metal surfaces appropriately.
- Apply coatings following best practices.
- Allow proper curing time.
- Conduct thorough inspections post-application.
- Implement a regular maintenance schedule.
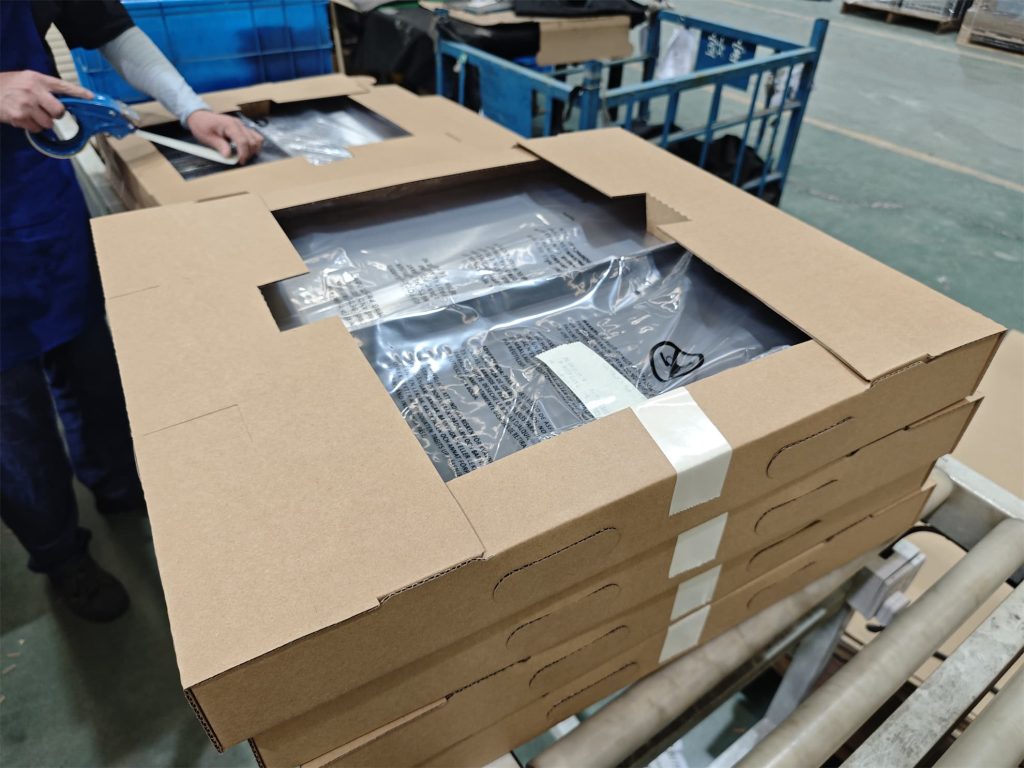
Conclusion
Adhering to established coating standards is vital for the durability and performance of metal parts in environmental equipment. By understanding and implementing these standards, manufacturers can ensure their products withstand harsh conditions, comply with regulations, and maintain operational efficiency.
FAQs
Q1: Why are coating standards important for environmental equipment?
A: They ensure metal parts resist corrosion, chemical exposure, and mechanical wear, enhancing durability and compliance.
Q2: How do I choose the right coating material?
A: Consider environmental conditions, operational requirements, and refer to standards like ISO 12944 for guidance.
Q3: What is the role of surface preparation in coating application?
A: Proper surface preparation ensures optimal adhesion and performance of the coating.
Q4: Are there specific standards for different types of equipment?
A: Yes, standards like NESHAP and ISO 12944 provide guidelines for various equipment and environmental conditions.
Q5: How often should coatings be inspected and maintained?
A: Regular inspections should be conducted as per the maintenance schedule, typically annually or as recommended by the coating manufacturer.