Table of contents
Introduction
In the realm of metal parts manufacturing, ensuring compliance with environmental regulations is paramount. The Restriction of Hazardous Substances (RoHS) directive stands as a critical standard, limiting the use of specific hazardous materials in electrical and electronic equipment. This guide delves into the intricacies of achieving RoHS compliance in metal parts manufacturing, offering insights into best practices, regulatory frameworks, and practical applications.
Understanding RoHS Compliance
RoHS compliance entails adhering to the European Union’s directive that restricts the use of certain hazardous substances in electrical and electronic equipment. For metal parts manufacturers, this means ensuring that products do not contain more than the permitted levels of substances like lead, mercury, cadmium, and hexavalent chromium.
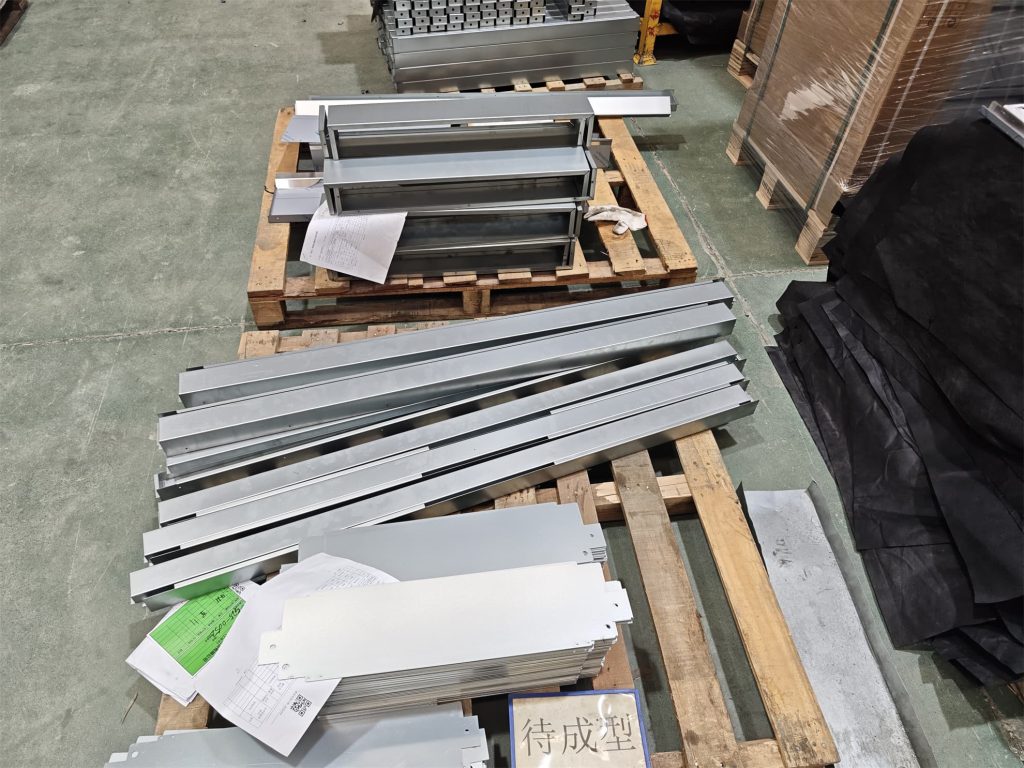
Key Restricted Substances and Limits:
Substance | Maximum Concentration |
---|---|
Lead (Pb) | 0.1% |
Mercury (Hg) | 0.1% |
Cadmium (Cd) | 0.01% |
Hexavalent Chromium | 0.1% |
Polybrominated Biphenyls (PBB) | 0.1% |
Polybrominated Diphenyl Ethers (PBDE) | 0.1% |
Understanding these limits is crucial for manufacturers aiming to produce RoHS-compliant metal parts.
Steps to Achieve RoHS Compliance
Achieving RoHS compliance involves a systematic approach:
- Material Assessment: Evaluate all materials used in manufacturing for the presence of restricted substances.
- Supplier Verification: Obtain declarations from suppliers confirming that their materials meet RoHS standards.
- Testing and Analysis: Conduct testing using methods like X-ray fluorescence (XRF) to detect hazardous substances.
- Documentation: Maintain comprehensive records, including test results and supplier declarations, to demonstrate compliance.
- Certification: Engage with certification bodies to obtain official RoHS compliance certification.
Implementing these steps ensures a robust compliance framework.
Common Challenges and Solutions
Manufacturers often face challenges in achieving RoHS compliance:
- Complex Supply Chains: Managing multiple suppliers increases the risk of non-compliant materials entering the production process. Solution: Establish stringent supplier evaluation and monitoring processes.
- Evolving Regulations: Staying updated with changes in RoHS directives can be daunting. Solution: Subscribe to regulatory updates and engage with industry associations for the latest information.
- Testing Limitations: Certain testing methods may not detect all restricted substances.Solution: Utilize a combination of testing methods and consult with accredited laboratories.
Addressing these challenges proactively is essential for compliance.
Case Study: Implementing RoHS Compliance
At our manufacturing facility, we embarked on the journey to RoHS compliance by first auditing our existing materials and processes. We discovered that some of our suppliers could not guarantee the absence of restricted substances. By sourcing new suppliers with RoHS certifications and investing in XRF testing equipment, we were able to ensure compliance across our product lines. This transition not only met regulatory requirements but also enhanced our market reputation.
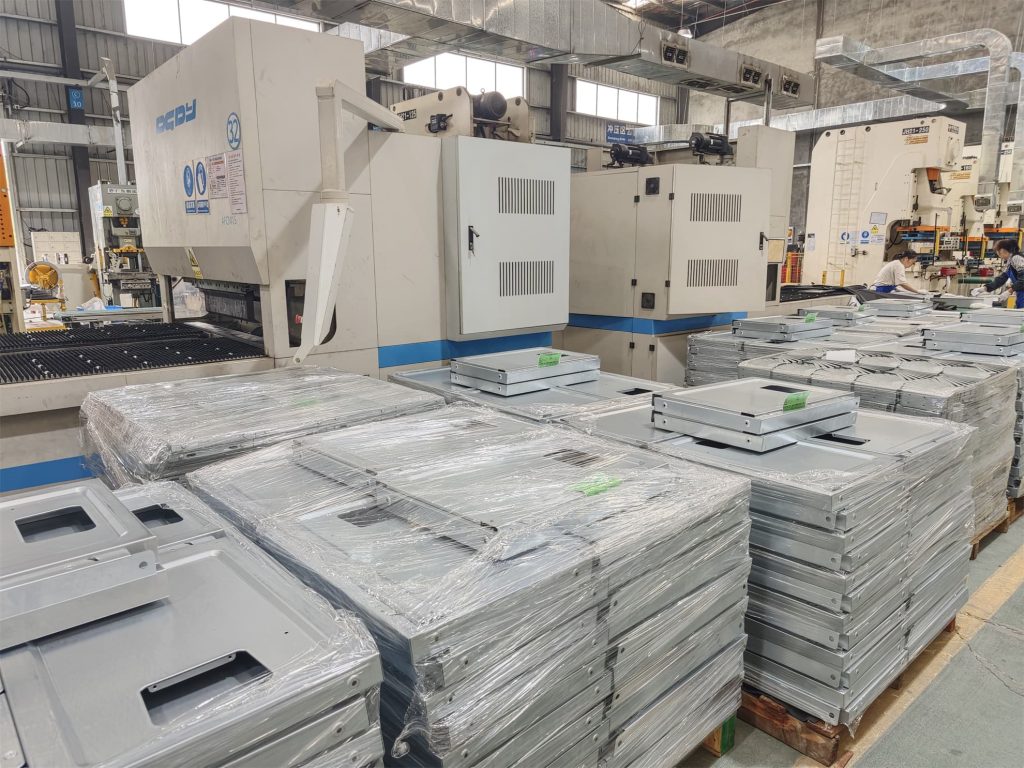
Best Practices for Sustained Compliance
To maintain RoHS compliance:
- Regular Training: Educate staff on RoHS requirements and updates.
- Continuous Monitoring: Implement ongoing testing and supplier assessments.
- Documentation Management: Utilize digital systems to manage compliance records efficiently.
Adopting these practices fosters a culture of compliance and quality.
Conclusion
Achieving RoHS compliance in metal parts manufacturing is a multifaceted process that requires diligence, collaboration, and continuous improvement. By understanding the regulations, implementing structured processes, and engaging with knowledgeable partners, manufacturers can not only comply with RoHS directives but also enhance their operational excellence and market competitiveness.
FAQs
Q1: What is RoHS compliance?
A: RoHS compliance refers to adhering to the European Union’s directive that restricts the use of specific hazardous substances in electrical and electronic equipment.
Q2: Why is RoHS compliance important in metal parts manufacturing?
A: It ensures products are safe for use, environmentally friendly, and meet international market requirements.
Q3: How can manufacturers test for RoHS compliance?
A: Through methods like X-ray fluorescence (XRF) analysis and consulting accredited laboratories for comprehensive testing.
Q4: What happens if a manufacturer fails to comply with RoHS?
A: Non-compliance can lead to legal penalties, product recalls, and loss of market access.
Q5: Are there exemptions to RoHS compliance?
A: Yes, certain applications and materials may be exempt, but it’s essential to consult the latest RoHS directive for specifics.
For expert guidance and support in achieving RoHS compliance, feel free to contact our team. We offer comprehensive solutions tailored to your manufacturing needs.