Why the Sheet Metal Process Directly Affects Product Quality, Lead Time, and Customer Satisfaction
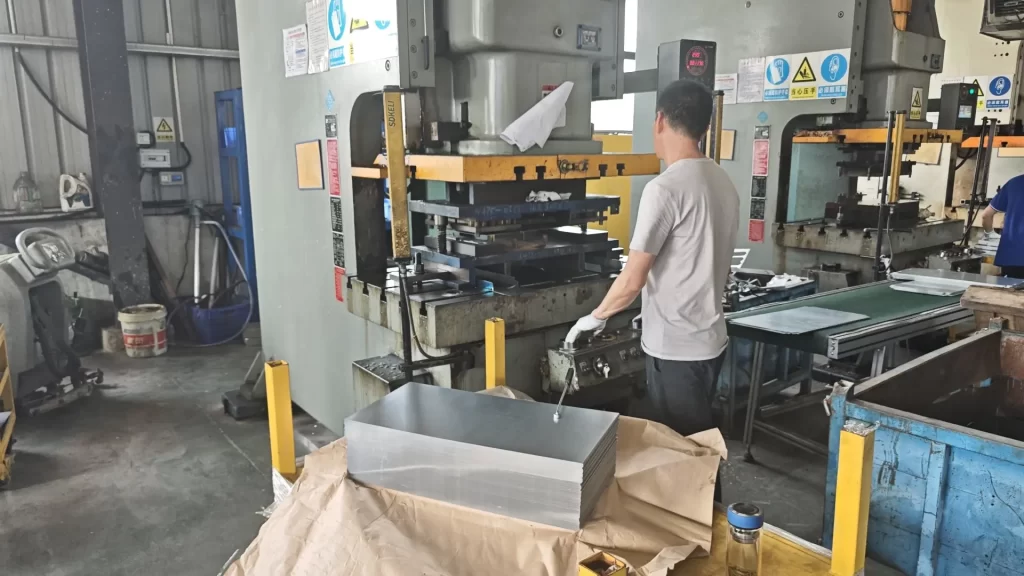
If you’ve been involved in metal fabrication, chances are you’ve encountered some “magical” moments—some so absurd, they make you question everything:
- “My drawings are perfectly fine, so why does the final product from the sheet metal factory look like a pile of scrap?”
- “Why does the metal surface look like it’s been licked by a tiger—covered in scratches?”
- “During assembly, parts either don’t fit or won’t go together at all—makes you want to kick the whole thing over.”
You’re not alone. And yes, we’ve all heard the saying in China: “Brute force creates miracles.”
In these moments, you’re drenched in sweat trying to fix things, the designer is shaking their head, the client is fuming, and your boss is busy apologizing. But the real problem is often not your design, nor the raw materials—it’s the sheet metal process itself, the very workflow you thought was simple.
The Process Isn’t What You Think
You may think the sheet metal process is just: turn on a machine → laser cut → bend → weld → done.
Let’s be clear—that is a huge misconception.
A true sheet metal process is an integrated system that spans from initial design and material selection, to cutting, bending, welding, quality control, and surface treatment. It’s a finely tuned chain of operations, and every stage must be standardized and tightly managed.
Any gap or flaw in this process can become an invisible landmine that causes late deliveries, part failures, or even lost clients. Many buyers don’t fully realize this until they’ve been burned by rework, delays, or angry customer complaints.
What This Article Will Teach You
Let’s bust a myth:
Sheet metal processing ≠ just messing with metal plates.
The purpose of this article is to guide you step by step through a professional, industry-grade sheet metal process—not the “cut-bend-weld-paint-go-home” version.
No, no. That’s completely wrong.
The real sheet metal process is a tightly linked fabrication chain, where every link affects the next—like gears in motion. Here’s what could go wrong when it’s not done right:
- Choose the wrong material? The entire batch may get scrapped right after production.
- Use the wrong cutting method? You’ll get blackened, warped edges.
- Bending angle off by just 1 degree? The assembly team might be crying all night.
- Welds not strong enough? The customer’s product breaks—and so does your business relationship.
- Poor surface treatment? The part rusts within a week of shipping.
These may seem like minor issues—but each one can determine whether you deliver on time, win the order, or lose your client forever.
How This Article Will Help You
This article uses plain language and practical insights to help you truly understand what a professional sheet metal process looks like from start to finish:
- From design and material selection to cutting methods—we cover it all.
- Which bending and welding techniques to choose? How to control tolerances? We’ll explain it clearly.
- What really matters in surface treatment? (Hint: it’s more than just the “color.”)
- And finally—what should a qualified sheet metal supplier do at each stage of the process?
You don’t need to be a technical expert, but you do need to understand this:
Sheet metal work is the art of metal precision—and it’s far more refined than you think.
So let’s start from the beginning—and understand the sheet metal process the way professionals do.
Step 1: Design and Process Review — Don’t Let Problems Start on the Drawing Board
If the sheet metal process is a manufacturing marathon, then your design is the way you position yourself at the starting line. Get that first step wrong, and no matter how fast you run afterward, it’s all in vain.
Many companies bring their CAD drawings straight to the factory, expecting a quick turnaround on finished parts. The drawings look beautiful—on screen. But once they enter the workshop, it quickly turns into a nightmare:
- “Our machines can’t bend this angle.”
- “No tolerance marked? Don’t blame us for the deviation.”
- “Is this structure from a dream? It’s not physically feasible.”
At first glance, you might think the factory is just being difficult. But in reality, you’ve embedded risk into your drawings!
Process Engineers Must Be Involved from the Start
In sheet metal fabrication, design for manufacturability (DFM) is not optional—it’s a hard rule. If you skip process validation, your “perfect” drawing is destined to fail on the shop floor.
Here are some common traps you might be falling into:
- Bend lines placed too close to edges? The die won’t fit.
- No bend radius allowance? Expect material cracks.
- Tiny holes arranged in a line? Laser burns and dimensional errors ahead.
- Complex welding structures? Heat distortion will keep you up at night.
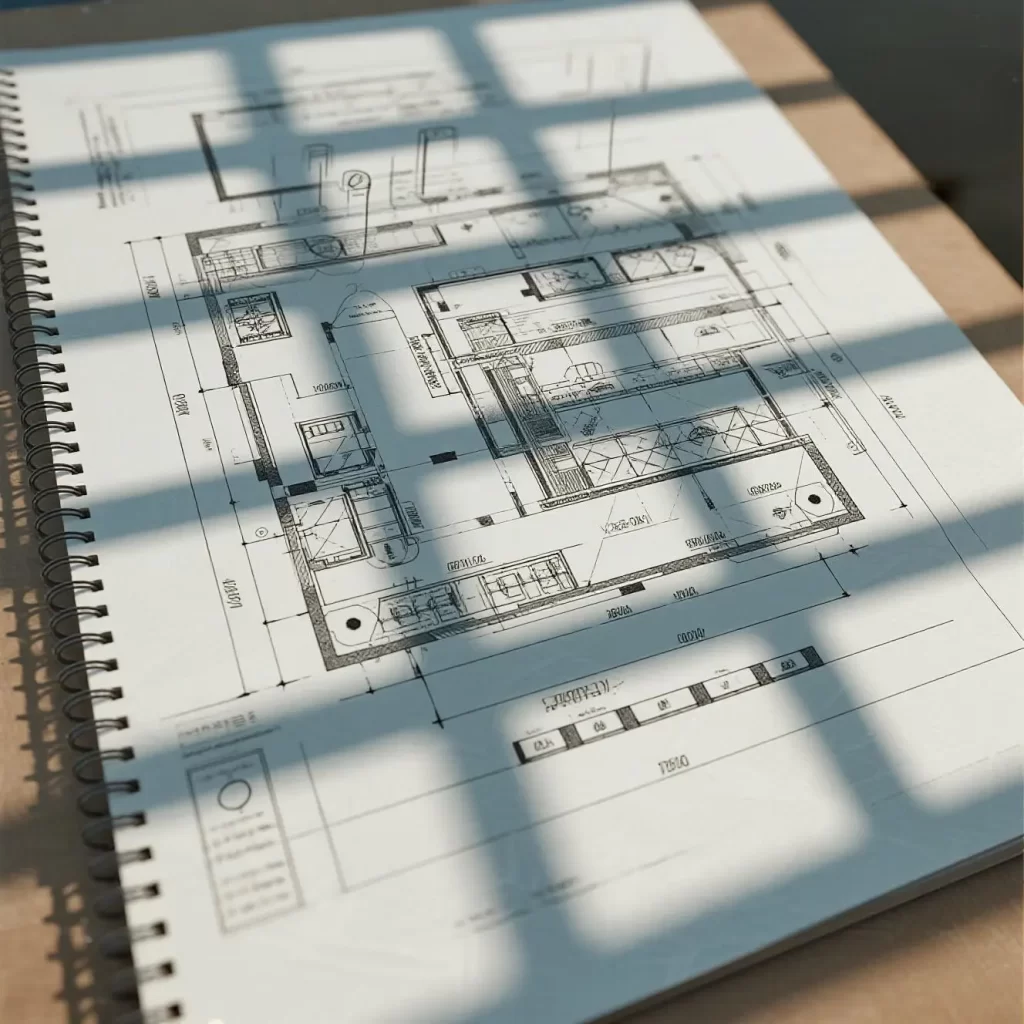
As highlighted by Protolabs:
“Designers must understand manufacturing. Otherwise, the most beautiful drawing is just a fantasy.”
If You Don’t Identify the Problems, They’ll Come Find You
A truly professional sheet metal supplier won’t just quote your drawing and move on. They’ll engage in early process reviews, provide modification suggestions, and flag designs that are headed straight for failure.
Suppliers who never mention DFM aren’t being “obedient”—they’re simply not professional.
If you dare to place the order, they won’t hesitate to send you a rework bill.
What Real Value Looks Like: Actionable Suggestions You Shouldn’t Ignore
Suggested Action | Why You Absolutely Need to Do It |
---|---|
Involve the factory during design | One mistake = three revisions = extra costs and lost lead time |
Use standard manufacturing parameters | Follow Protolabs or Xometry guidelines—avoid rookie mistakes |
Conduct a DFM check before finalizing | A 0.2mm tolerance issue could destroy your entire production batch |
Always prototype seriously | Better to fail on 10 parts than 10,000. Trial saves disasters |
Gaining an in-depth understanding of various Common Materials in Sheet Metal Fabrication ensures that the direction of material selection matches subsequent processes such as cutting and bending.
Step 2: Cutting Process — Never Underestimate the Power of a Single Cut
Many assume cutting is simple:
“Isn’t it just laser, punching, or shearing? Pick one and move on.”
Sorry, but you’re drastically underestimating it.
In the sheet metal process, the cutting phase is more than slicing through steel. It determines your product yield, assembly precision, and ultimately, your bottom line.
Cutting Process — The First Gate That Defines Quality Potential
If design is the strategic plan, then the cutting process is the tactical execution that determines your product’s future. Choose the wrong method, and you’ll spend the rest of the sheet metal process cleaning up the mess—expensive, time-consuming, and avoidable.
According to Xometry’s latest Sheet Cutting Design Guide (PDF), your cutting method should be based on material thickness, shape complexity, and edge quality. The goal? Finding the balance between precision and heat-affected zones.
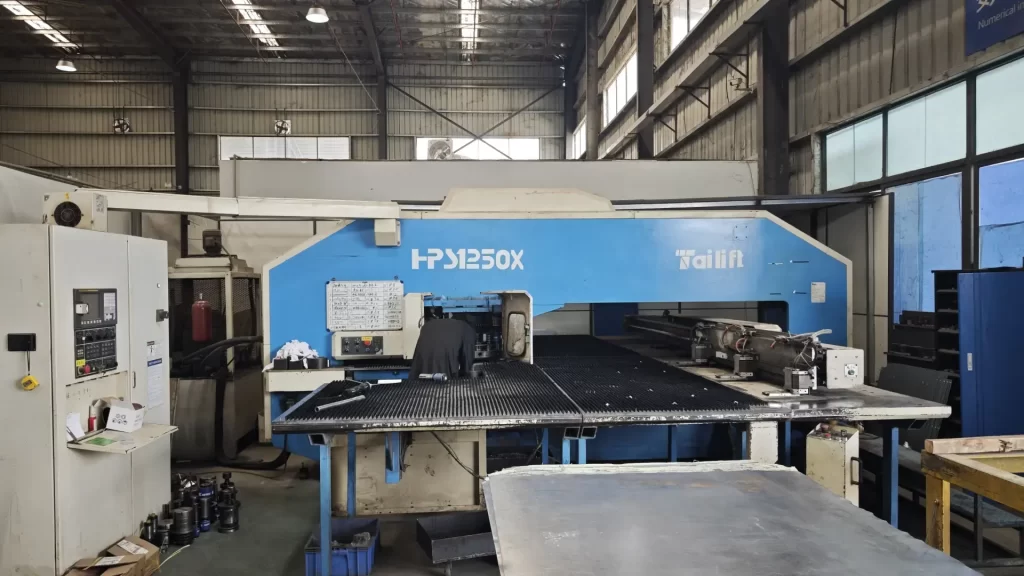
Pros and Cons of Common Cutting Methods
Cutting Method | Advantages | Limitations & Risks |
---|---|---|
Laser Cutting | High precision, supports complex contours | Risk of burns on thicker plates, relatively costly |
CNC Punching | Fast for high-volume repetitive parts | Expensive tooling, limited shape flexibility |
Shearing | Low cost, great for straight-line cutting | Can’t handle curves or holes, limited precision |
Plasma/Flame | Suited for thick sheets, affordable machines | Low precision, significant thermal distortion |
You may think you’re just choosing a tool, but what you’re really deciding is:
- Can this batch be delivered on time?
- Will the customer be satisfied?
- Can we preserve any profit?
If you want to learn more about the integrated processing advantages of CNC Punching + Laser Cutting, you can check out our detailed process introduction to Numerical Control Discrete Parts Processing.
Poor Cutting = Digging Your Own Grave
A deviation of just ±0.3 mm can spell disaster. It throws off bending alignment, leads to weld gaps, and jammed assemblies. And when your customer opens the crate, they’ll ask:
“Was this product made for me, or for fun?”
As Xometry warns:
“When cutting deviation exceeds ±0.25 mm early on, downstream rework rates can surge by over 50%.”
Never underestimate the cost of a few cents of error. It’s the tip of a catastrophic iceberg.
Must-Do Actions for Professional Sheet Metal Cutting
Action | Why It Matters |
---|---|
Use properly calibrated CNC machines | Old machines = unreliable output |
Set accurate programming parameters | Cutting path, speed, and heat compensation must be optimized |
First-piece inspection is a must | If the first cut is wrong, stop everything! |
Follow standardized material handling | Proper stacking, securing, and flattening ensure cut accuracy |
If you skip these, your delivery outcome depends more on luck than on expertise.
Recommended Checklist for Cutting Success
Action | Why You Can’t Skip It |
---|---|
Choose cutting method wisely | Each is suitable for different shapes, thicknesses, and volumes |
Validate parameters (spacing, compensation, sequence) | One mistake = entire batch rework |
First-batch inspection post-cutting | Catch issues before mass production |
Prefer multi-method-capable suppliers | Reduces outsourcing, improves consistency, saves cost |
Step 3: Bending Process — If This Step Fails, the Structure Collapses
Think bending is just “pressing a sheet into a curve”? Think again.
The bending process in the sheet metal process is far more complex than it appears. Mismanaged bends result in assembly errors, instability, and wasted material.
Why Bending is a Make-or-Break Step
- Springback: Metal “bounces back” after being bent, making angles inaccurate.
- Cracks & Wrinkles: Wrong tool or force = surface damage or material failure.
- Angle Inconsistency: Unstable equipment or manual bending = batch variation.
What the Experts Say
- According to Wikipedia, springback is normal. Compensate by over-bending based on material properties and equipment specs.
- Protocase recommends: Inner bend radius ≥ sheet thickness and bend angle tolerance within ±1°—this is now industry standard.
- Fractory advises: Always include bend reliefs (notches) to avoid tearing or material distortion.
- Geomiq emphasizes the role of simulation tools in predicting accurate bend outcomes.
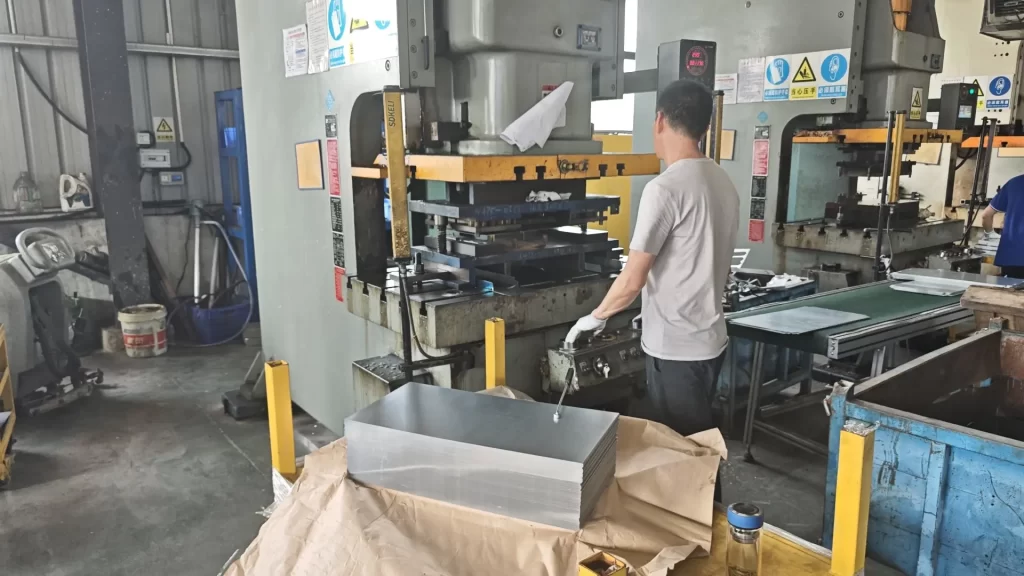
Poor Bending = Structural Instability
If the bending process goes wrong, no amount of downstream correction will save your structure. Uneven angles mean:
- Poor fit during assembly
- Visible deformation
- Higher rejection rates
The best sheet metal suppliers know this—and they use proper tools, bend calculations, and material-specific compensation from the first trial bend.
Sheet Metal Bending – Accuracy and Stability Start Here
Think bending is simple? Think again. In the sheet metal fabrication process, bending isn’t just about “making a curve”—it’s the structural backbone of the final part. Done well, everything fits. Done poorly, the entire assembly fails.
What Makes a Professional Sheet Metal Bending Process?
1. Select the Right Bending Die (V-die or U-die)
Tool width and shape must match material thickness to prevent cracks and wrinkles.
New Mexico Metals emphasizes that improper die selection is the top cause of bending defects.
2. Apply Proper Bend Compensation
Calculate springback compensation using the K-factor (typically 0.3–0.5) to ensure post-bend angles are correct.
Sources like Geomiq and Wikipedia recommend precise simulation for K-factor estimation.
3. Stabilize the Workpiece
The press brake must remain level, and the sheet should stay in fixed position—use back gauges and clamps if needed to avoid shifting.
4. First-Piece and Batch Inspection
Measure the first bent part immediately to verify angle and dimensions. Then continue in-process inspections during batch production to prevent drift.
What Happens If Bending Is Poorly Done?
- Excessive angle deviation → Misalignment with casings or holes = unusable part.
- Too-narrow bend → Cracks form, structural integrity fails.
- Material slips during bending → Angle inconsistency, costly rework.
Even a ±1° angle deviation can severely affect assembly precision and mechanical strength.
Expert Checklist for Accurate Sheet Metal Bending
Must-Do Steps | Why It’s Critical |
---|---|
Inner bend radius ≥ sheet thickness | Prevents cracking and deformation |
Angle tolerance within ±1° | Ensures batch consistency |
Die and material must be matched | Avoids surface defects like folds and splits |
Use ISO/CE certified bending machines | Reduces human error |
Establish first-piece + batch QA | Catch deviations early to minimize waste |
Bending defines the shape. Stability and precision start here. Get this wrong, and the whole structure suffers.
Step 4: Welding & Assembly — Without Stability, It All Falls Apart
To make individual sheet metal parts into a unified product, you need welding. But welding isn’t just about joining—it determines strength, reliability, and appearance. Get it wrong, and the structure may collapse like a house of cards.
Why Welding Thin Sheet Metal is Challenging
- Thin material burns through easily if too much heat is applied.
- Heat distortion can twist the part, compromising structural balance.
- Joint strength is directly tied to technique—choose wrong, and it won’t hold.
Common Welding Methods & Comparisons
Welding Type | Advantages | Cautions |
---|---|---|
MIG | Fast, suitable for thin sheets | Shielding gas is vulnerable to wind—can reduce quality |
TIG | Clean seams, precise control | Slow, high skill requirement |
Spot Welding | No filler needed, ideal for overlap joints | Low strength—best for light-load applications |
Lap Fillet Arc | High strength for edge joints | Large heat-affected zone; prone to distortion |
Must-Know Sheet Metal Welding Techniques
1. Start with Tack Welding + Follow with Full Pass
Use skip welding to distribute heat and minimize warping.
Recommended by Wayken
2. Choose the Right Filler Wire + Shielding Gas
- Filler diameter should be slightly smaller than sheet thickness.
- Use 75% Argon + 25% CO₂ for steel welding (Miller Welds)
- For stainless steel, use Argon + Helium + CO₂ for stability and aesthetics.
3. Control Heat Input
Apply low amperage and fast travel speed to avoid distortion.
As advised by ESAB
4. Post-Weld Cleanup is Non-Negotiable
Immediately remove spatter and slag via grinding or pickling.
Even functional parts should look polished and professional.
Highlighted by Geomiq and KDMFab
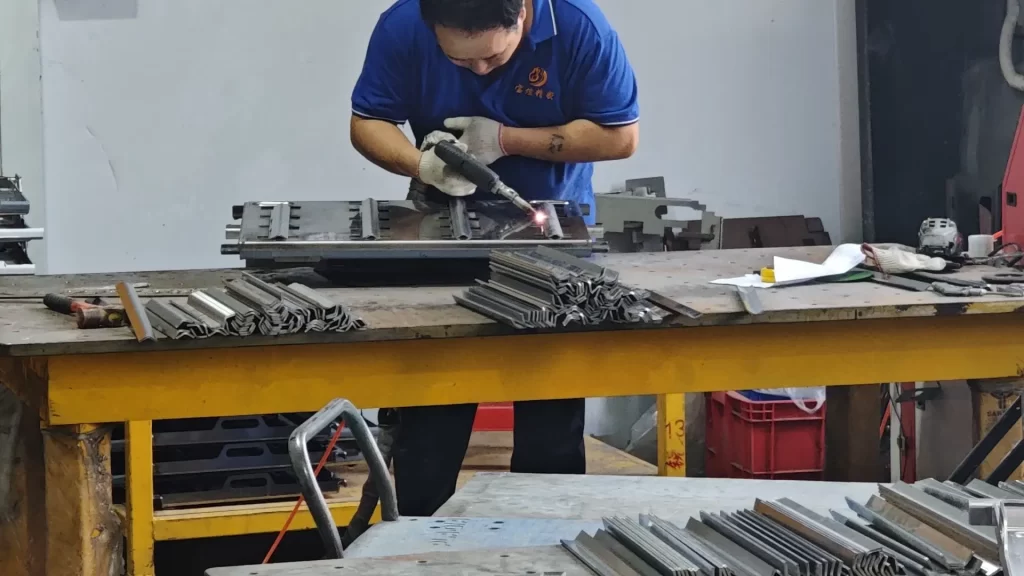
Assembly Interface – The Hidden Heroes of Sheet Metal Fit
When it comes to final assembly, details like fasteners, snap-fit structures, and fixture jigs may seem minor—but they define precision, repeatability, and long-term strength. Miss this step, and your structure may never come together as designed.
Key Assembly Features to Include
- Snap-fit / Latch Structures – Speed up assembly while adding mechanical strength.
- PEM Studs / Fastener Inserts – Enhance automation and post-punch integration.
- Assembly Fixtures – Maintain dimensional consistency across high-volume batches.
- Welded-Part Validation – After welding, compare final dimensions with CAD drawings to prevent cumulative errors.
Poor Welding = High Cost Failures
- Burn-through the sheet? → Part is scrap.
- Cracked welds? → Customer returns upon delivery.
- Distorted weld zones? → Assembly misalignment, total rejection.
A weld bead may cost a few cents—but a failed weld can cost you thousands in rework, reputation, and lost business.
Expert Welding Quality Checklist
Step | Must-Do Action |
---|---|
First-Piece Verification | Measure, photograph, and archive the first welded part. |
Welding Parameters Traceability | Record wire type, voltage, current, and travel speed. |
Ongoing QA | Spot-check batches, document images, catch errors early. |
Select Welding Process by Function | MIG for structural parts, TIG for ultra-thin parts, spot welds for small latches. |
This step defines strength + aesthetics + consistency. Master welding, and you master quality.
For high-end applications, it is recommended to refer to our Drone sheet metal welding guide to learn about the practice of advanced welding technologies such as CMT and Micro‑Plasma in the welding of ultra-thin sheets.
Step 5: Coating & Finishing – It’s Not Just About Looking Good
Some clients say: “I just want it painted—looks fine to me.”
But a few months later? Peeling, rusting, and angry phone calls.
Surface finishing in sheet metal isn’t just for aesthetics. It ensures long-term durability, corrosion resistance, electrical performance, and even customer perception. Skipping this step can turn a great product into a costly failure.
Why Surface Finishing Matters
- Corrosion Protection – Bare steel rusts quickly, especially outdoors.
- Wear Resistance – Industrial parts face constant friction and contact.
- Electrical Insulation or Conductivity – Some enclosures require EMI shielding or isolation.
- Brand & Aesthetic Appeal – First impressions count; premium coatings elevate perceived value.
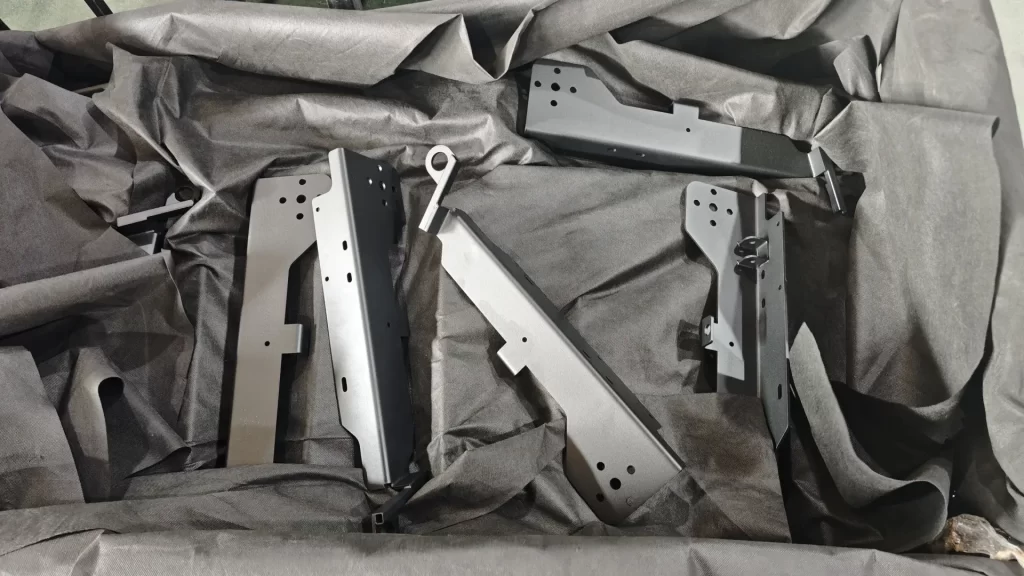
Common Finishing Techniques & Tradeoffs
Process | Pros | Key Notes |
---|---|---|
Powder Coating | Durable, scratch-resistant, colorful | Requires pretreatment and curing under high heat. [SAF.com, Komaspec] |
Anodizing (for aluminum) | Hardens surface, corrosion-resistant, elegant look | Affects dimension; sealing prevents porosity. |
Chemical Film / Chromate | Rust-resistant, maintains conductivity | Thin layer, easily scratched, usually as a base coat. |
Bead Blasting | Matte texture, removes burrs, improves adhesion | Grit size affects finish; requires proper PPE. |
Pro Finishing Tips You Can Use
- Match finish to environment: Powder coating for indoor cabinets; anodize + coat for outdoor gear.
- Material determines method: Aluminum? Anodize it. Galvanized steel? Powder coat holds better.
- Mind the thickness: Powder coat adds 0.05–0.15 mm; anodizing adds 0.01–0.05 mm.
- Leave tolerance gaps: Finishing affects fit—adjust part dimensions accordingly.
- Color matching requires sampling: Ensure batch-to-batch consistency via strict process control.
If you need to understand the coating standards and surface treatment requirements for specific industries (such as BBQ, communications), you can read our case sharing on Why Powder Coating Is Essential for BBQ Grill Brackets.
Finishing Selection Quick Guide
Use Case | Recommended Finish | Why It Works |
---|---|---|
Outdoor weatherproofing | Anodizing + fine powder coat | Corrosion protection + lasting appearance |
Home appliances, showcases | Powder coating | Rich color options and uniform feel |
Electrical enclosures | Chemical film + powder | Rust-proof base with excellent adhesion |
Industrial tools, anti-slip | Bead blasting | Matte grip + de-burring |
Risks of Skipping Proper Finishing
- Poor powder coat → Peeling in months, product returns.
- Bad anodizing → Electrical short circuits, failed insulation.
- Unsealed chromate → Moisture seeps in, corrosion starts.
- Rough blasting → Unprofessional texture, rejected by customers.
Step 6: Quality Control & Tolerances – A Wrong Mark Can Ruin It All
A well-crafted drawing and sophisticated process mean nothing if quality control fails. In this section, we’ll explain how to make sure every single sheet metal part that leaves your shop is truly qualified.
Why Quality Control Is Non-Negotiable
- Cumulative Tolerances: Each process introduces slight deviations—without control, they stack up to serious failures.
- Hidden Defects: Bending cracks, weak welds, or poor coating adhesion may not show immediately but explode at the customer site.
- High-Stakes Clients: Automotive, medical, and aerospace sectors reject anything substandard—one flaw, one return.
Industry Insights
- “Clear quality definitions and inspection points in key operations are the foundation of sheet metal control.”
- “Trained staff + calibrated equipment + process monitoring = quality trifecta.”
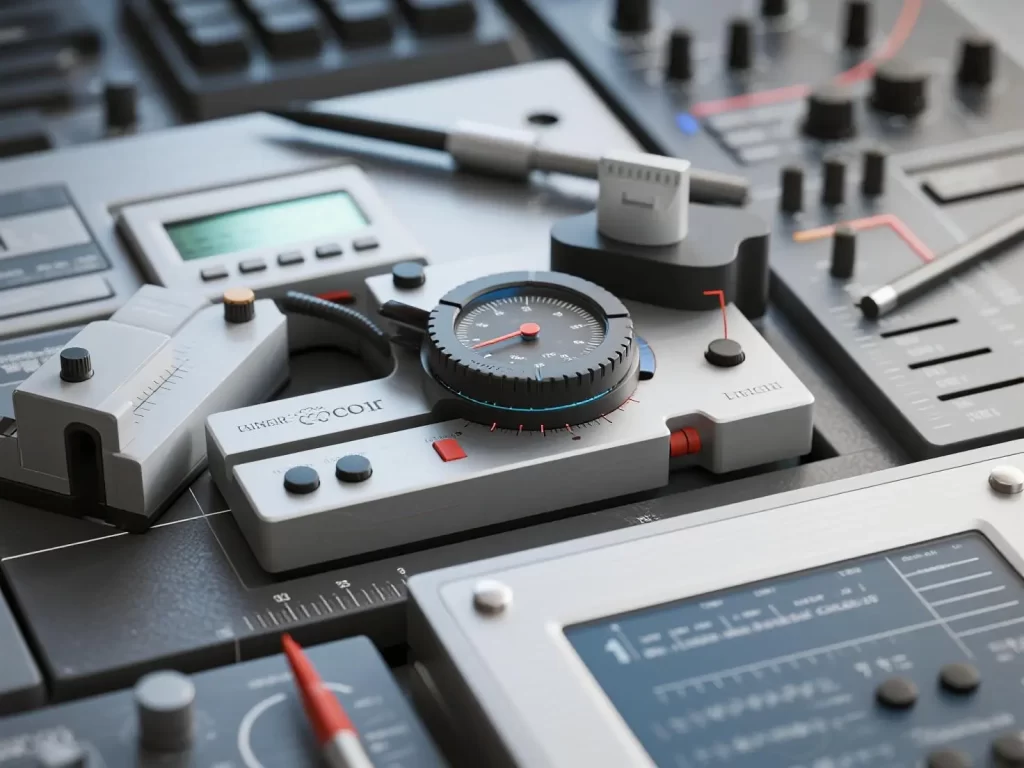
Core Quality Control Workflow
Phase | Key Actions |
---|---|
Establish Standards | Define size, material, surface, welds, tolerances—set red lines clearly. |
Machine + Operator Calibration | Regularly calibrate lasers, benders, welders; train operators to avoid errors. |
First Article + Batch + Final Inspections | Measure the first piece, sample mid-batch, and inspect before shipping. |
Tolerance Management | Typical sheet metal tolerance: ±0.1–0.2 mm; bending: ±1° per Protolabs, Komacut. |
Weld + Structural Inspections | Use ISO/ASME methods like ultrasonic, magnetic particle, or dye penetrant NDT; meet API or EN 1090 standards where required. |
Pro Tips for Tight Tolerance Control
- Leave allowance in design: Avoid stack-up errors.
- Apply GD&T in CAD drawings: Convey tolerance intent clearly.
- Use CMM / coordinate measuring machines: Ensure traceable accuracy.
- Build repeatable processes: Staff manuals + process feedback loops = consistent quality.
Summary Table
Must-Do | Why It Matters |
---|---|
Written quality standards + checklists | No rules = No execution |
Periodic equipment calibration + training | Poor setup = poor output |
First-article + batch + final inspections | Catch issues early, not post-shipment |
Tolerance control (±0.1–0.2 mm, ±1°) | Over = scrap; under = rework |
Weld NDT inspections (ISO/API, etc.) | Unchecked = invisible danger |
Quality is not about ticking boxes—it’s about building trust, part by part.
Process Optimization Tips – Faster Is Only Better When It’s Also Stable
Speed alone won’t cut it. The key is to build efficient, standardized process flows that are both fast and reliable.
1. Multi-Process Integration
Avoid sending each task to a separate department. The best results come from single-stop solutions.
“From design to finishing, our team acts as an extension of yours—cutting costs and timelines.”
✔ Benefits:
- Less transport cost
- Faster turnaround
- Fewer hand-off errors
2. Design-to-Manufacture Collaboration
Early-stage collaboration avoids costly rework. Here’s how clients can help:
- Clarify quantity: Prototype or mass production?
- Share material specs & tooling constraints
- Use DFM (Design for Manufacturing) reviews—follow Komacut or Xometry practices
- Use CAD simulations + CAM feedback for rapid iteration
One design tweak now = avoiding five reworks later.
3. Smart Manufacturing & Automation
Modern workshops use CAM + IoT to monitor efficiency in real-time and reduce downtime.
“Process optimization means linking CAD → CAM → machine in one loop.”
✔ Results:
- Quicker delivery
- Fewer errors
- Happier workers
Conclusion: Why Choose a Truly Professional Sheet Metal Partner?
Expert Team + Full Process Support
A real partner offers more than cutting and bending—they understand the full workflow from design to coating to delivery.
advanced technical knowledge, with dedicated engineers and production managers.
Delivery Assurance + Custom Workflow
Professional shops have defined production lines, ISO-level monitoring, and tight quality loops. That means:
- Reliable timelines
- Controllable quality
- Scalable output
One-stop integration includes not only cutting, bending, welding, but also processes such as stamping, deep drawing. For details, please refer to the process diagrams in our article “OEM sheet metal fabrication Top 6 Solutions“.
Final Words
Sheet metal fabrication isn’t just cutting and bending—each step carries its own risks. From early design review to integrated workflows, tolerance control, and finishing, every step matters.
Choose a partner who:
- Understands your product
- Prevents problems early
- Delivers consistent quality
- Meets deadlines
- Saves your total cost
Ready to unlock your custom fabrication process, CAD review, or instant quote?
[Contact Us Now] – Get high-quality production, fast delivery, and zero-stress support!